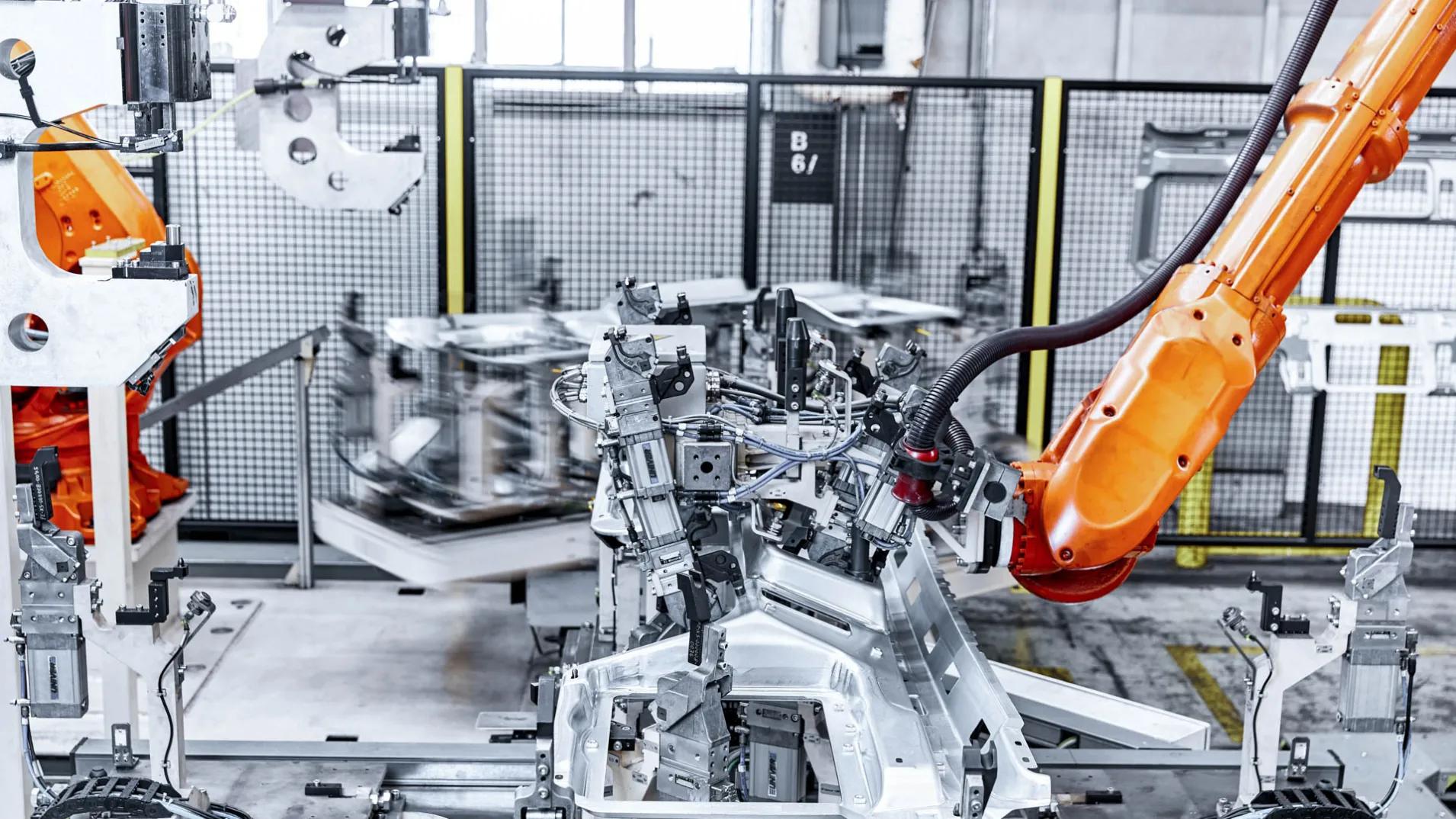
OEM reference
Increased cycle times for more productivity
HÖRMANN Intralogistics Services carried out an increase in cycle time and optimization of the workplace in the assembly plant of an OEM, taking into account ergonomic and ecological aspects. With the customer a concept was developed, which improves the loading and unloading of two parallel machines for processing components.
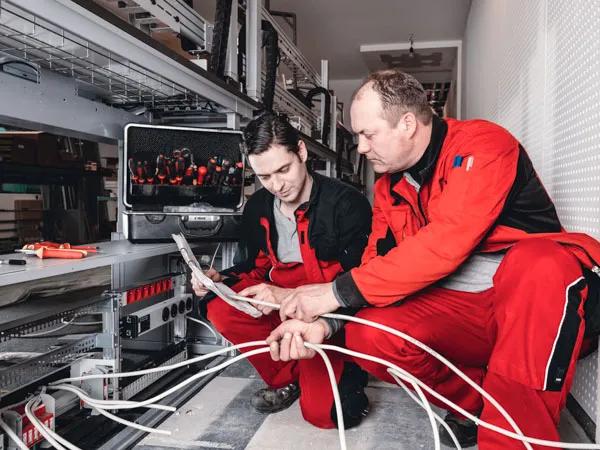
The components had to be deposited in the machine beforehand via loading gantries. Loading and unloading could only take place one after the other: first machine 1, then back and forth, and then machine 2. After unloading, the loading gantries had to make an empty run back into the component removal area to be loaded with a new component. During this process, the machine was unable to continue processing a component - this led to high downtimes.
This process is now carried out by two robots that can load both machines in a staggered manner. The transport distance was reduced by a smaller swivel radius from component removal to placement. The components can now be transported in parallel and simultaneously. There are no more waiting times.
"With the new concept, we created short distances and lower costs due to downtimes for machine and line operators with up to a threefold time improvement"
GERHARD JACOBI | EXECUTIVE DIRECTOR
Good reputation leads to follow-up projects
"The customer commissioned the project from us not only from an economic point of view, but also because of our experience and our good references in the field of automation," Gerhard Jacobi continues. Another plus point was that there were no interface problems, as HÖRMANN Intralogistics Services was able to offer the entire project from A to Z - from planning, concept development, design, data backup, automation to mechanics and electrics. Thanks to the year-round presence on site, the HÖRMANN Intralogistics Services employees were immediately available in case of adjustments.
So immediately afterwards, the customer commissioned another project to improve component production. In the future, the handling of the shopping baskets on the cockpit assembly lines, which contain components and are transported to logistics by a sequence trolley, will also be handled by robots. In the past, the baskets were loaded by hand - this often led to time problems and, as a result, downtime in final assembly.
"The baskets are now fully loaded just-in-time at the assembly lines, matching the corresponding vehicle"
GERHARD JACOBI | EXECUTIVE DIRECTOR
All-round service for a smooth process
The design and fabrication of the gripper technology for the robot was created by the employees of HÖRMANN Intralogistics Services. Through a Robcad survey, the positions of the robots and the new work area were determined. Planning was followed by assembly and installation with robot consoles, energy supply, media supply, lighting, cabling, pneumatics and grippers.
Tailored for the customer, a steel maintenance platform was fabricated and assembled with access, stairs, railings and guards, as well as light barrier technology. Then followed the programming and commissioning of the robots as well as the coordination of the internal interfaces of the robots to the plant. "We basically accompany the production for a few weeks in order to eliminate possible malfunctions directly and to train the plant operators on site during operation," says Gerhard Jacobi.
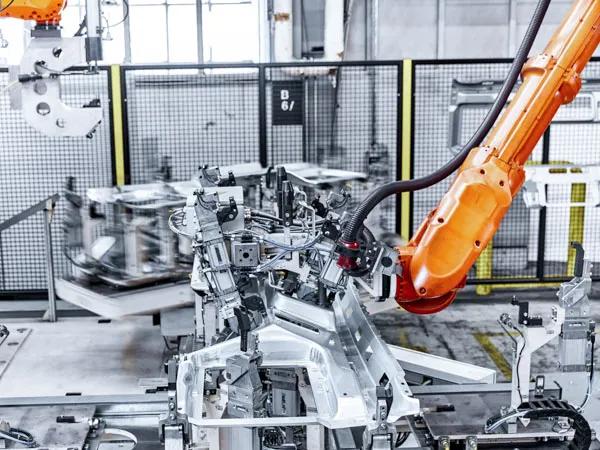