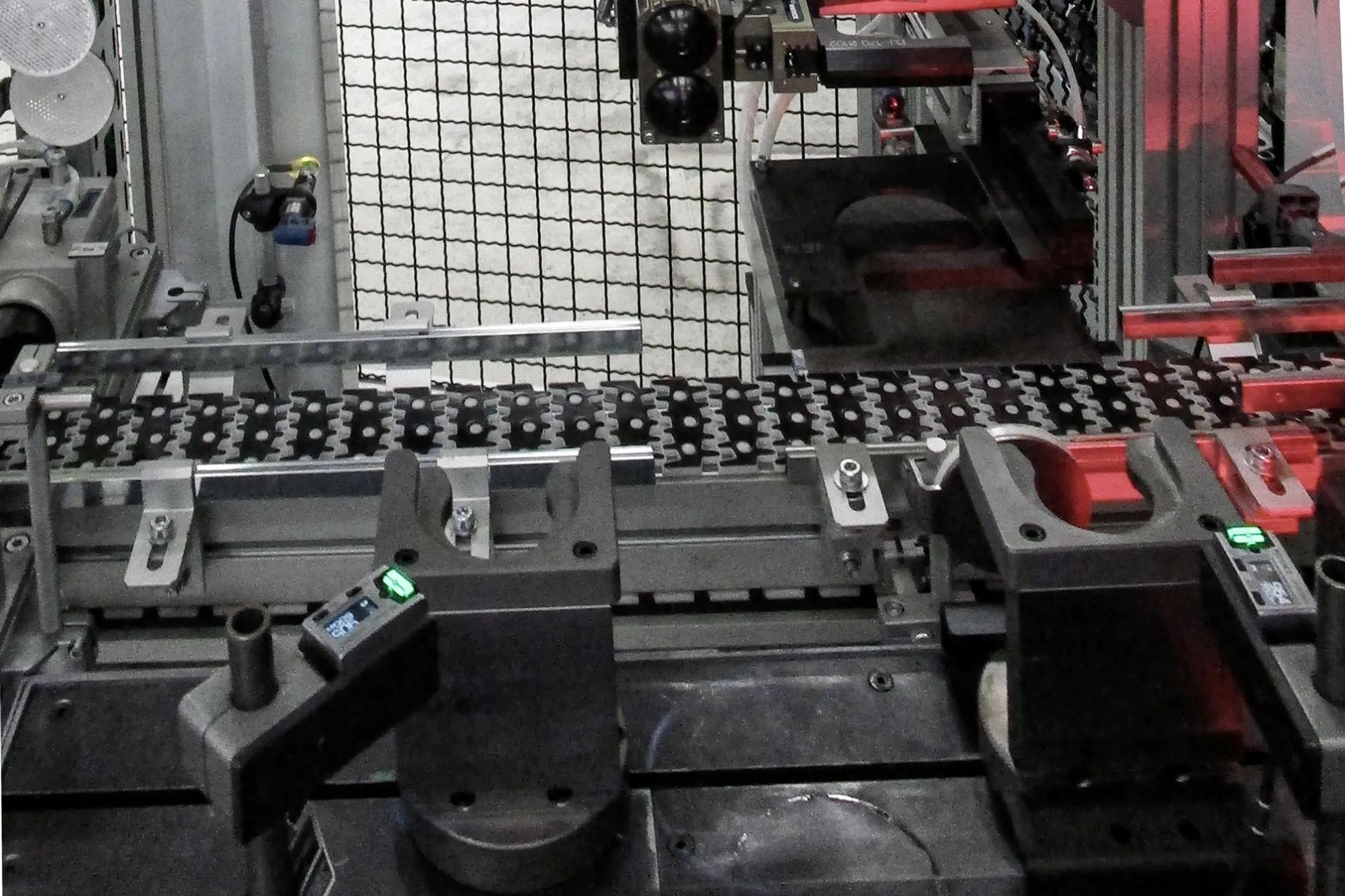
Reference NTN Drive Technology
Reliability at the right pace during transport through series production
For the assembly of a modern automobile with an internal combustion engine, up to 10,000 components are required, which are produced in highly automated, clocked production lines with a high number of processing stations and a wide variety of manufacturing processes. To ensure high economic efficiency of these production facilities associated with multi-million investments, the reliable transport of components from station to station in the right cycle is of particular importance.
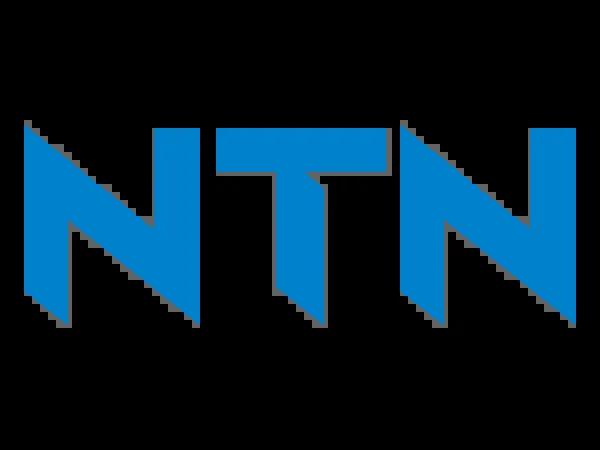
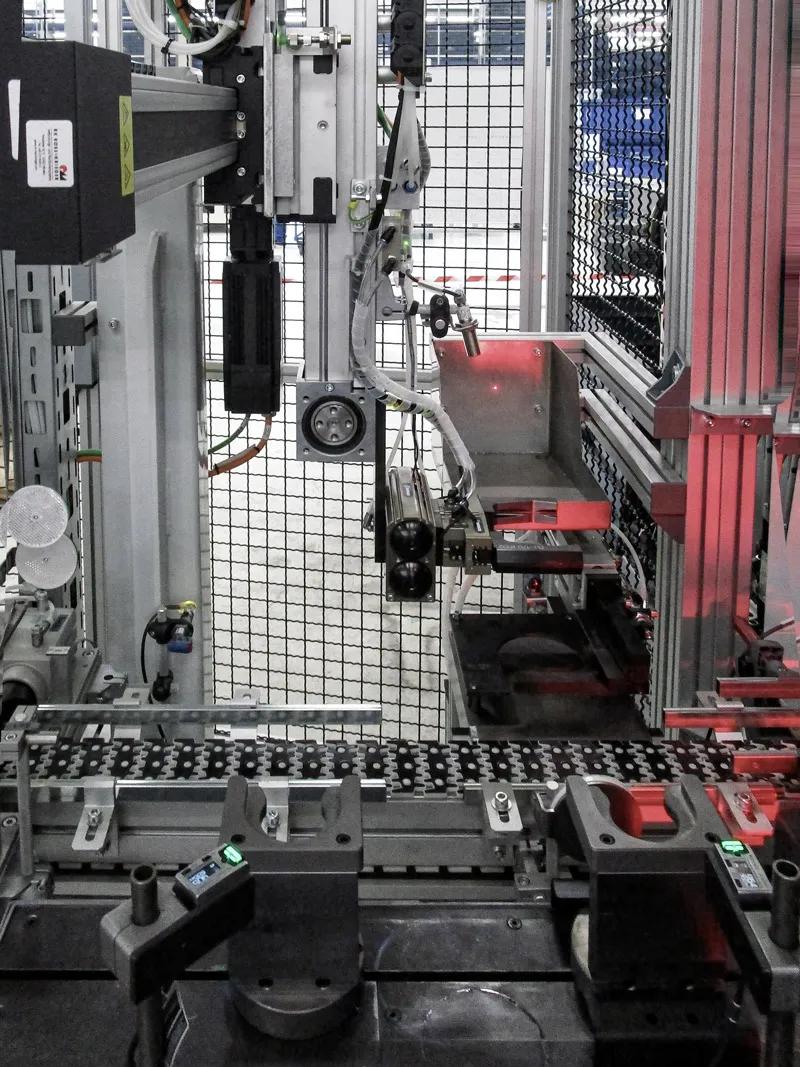
NTN Antriebstechnik GmbH in Gardelegen (Saxony-Anhalt), a subsidiary of the Japanese NTN Corporation, is a leading global producer of drive shafts for the automotive industry and a supplier to well-known German car manufacturers. In connection with the construction of two new production lines, NTN commissioned HÖRMANN Intralogistics with the interlinking of the individual processing stations. In this project, demanding goals had to be realized: a line cycle of 36 seconds and an output of 800 parts per shift.
Turnkey automated production systems from a single source
HÖRMANN Intralogistics created the plant layout, the mechanical design of the linkage, and the automation concept, including electrical planning. At the heart of the interlinking are the hinged chain conveyors, the loading gantries/stations that transport workpieces weighing a maximum of 2.2 kilograms. Particular challenges in the project planning were the integration of a tempering furnace for heat treatment of the workpieces and the guarantee of a travel path in the production by means of a lifting/lowering station.
The installation of the mechanical components, all protective devices and the electrical installation were carried out by HÖRMANN Intralogistics Services GmbH, a business unit of HÖRMANN Intralogistics.
The automation technology and software developed in-house ensure precisely timed control of the entire transport from station to station with a high level of availability, whereby each production line has a separate control system with a high number of protective circuits. Numerous services accompanying the product, such as the inspection of electrical equipment in accordance with DGUV 3, training of operating and maintenance personnel, commissioning of the system, support during the start of production, as well as the usual documentation, operating instructions and maintenance plans, complete the scope of services provided by HÖRMANN Intralogistics.
After several changes in the parts spectrum, the successful commissioning of the entire production plant took place at the beginning of 2020.
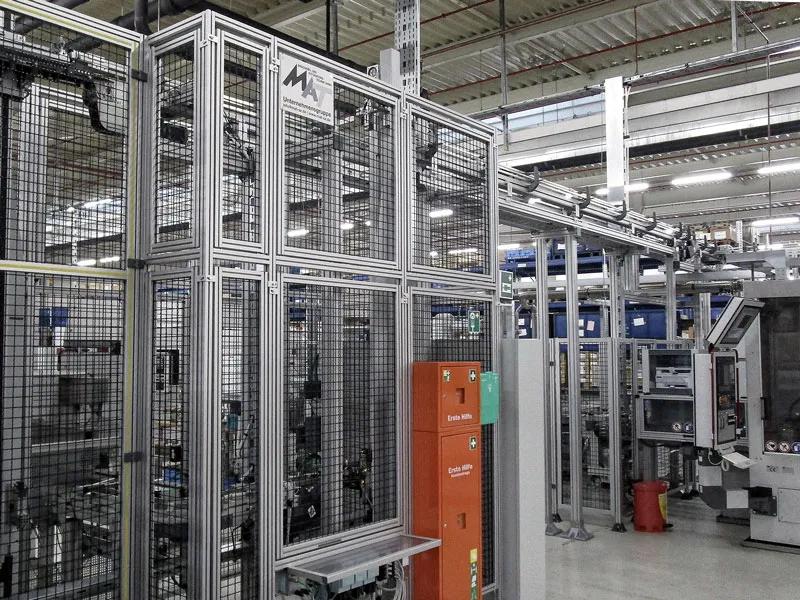