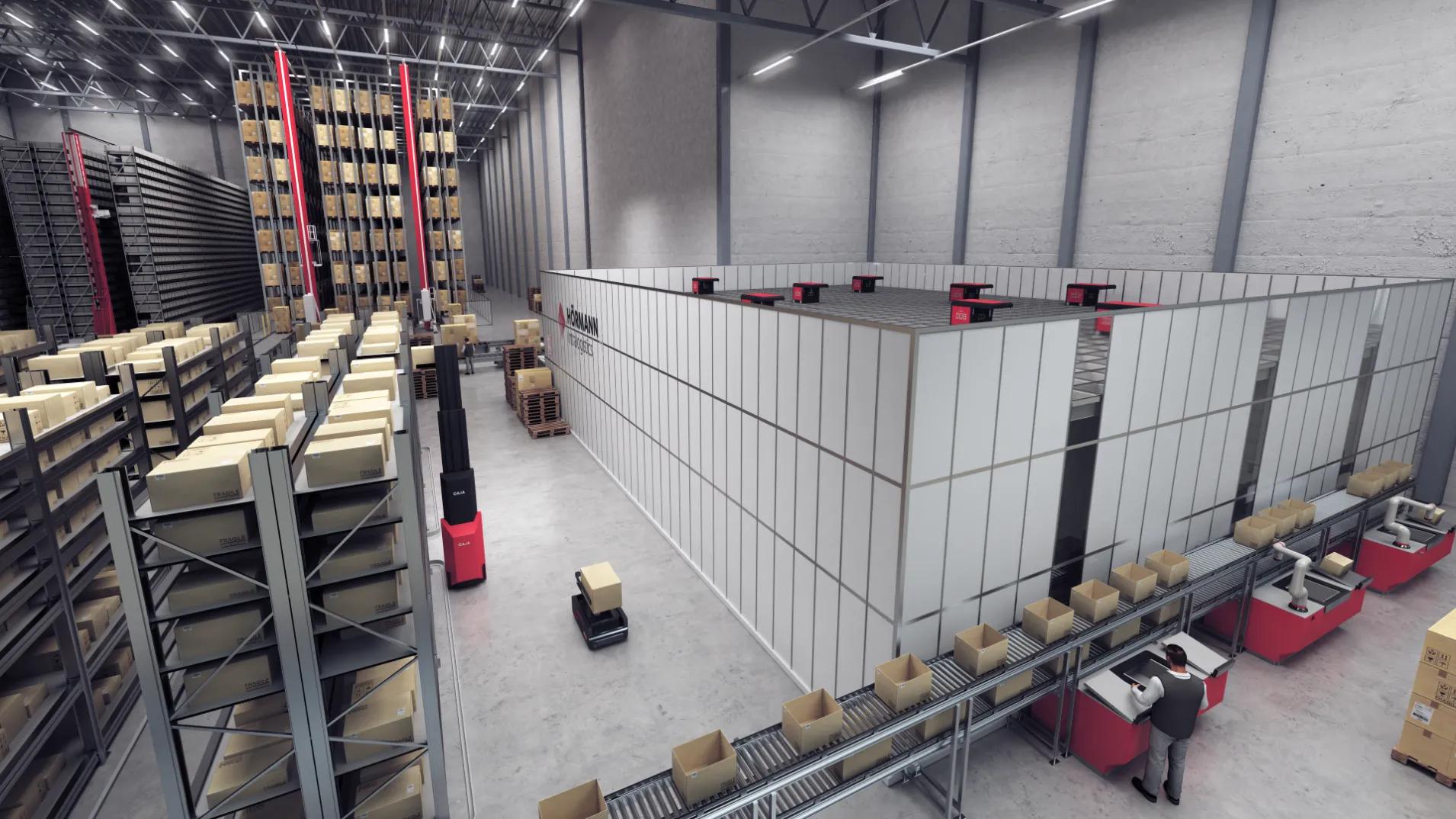
Innovative multi-solution material flow solutions
Smart integrated warehousing
With individual, creative multi-solution intralogistics systems, we implement efficient and future-proof material flow solutions for various industries. We design and combine automated high-bay warehouses, tray and small parts/light goods warehouses, AutoStore® systems and picking systems specifically for your requirements to ensure maximum productivity for our customers.
Depending on the industry, volume, product characteristics, range, logistics property and required throughput, we can recommend and install the right autonomous solution for you. As a general contractor, we bear overall responsibility for implementation and are at your side with a single point of contact from planning to commissioning.
The overall system is integrated with HiLIS, our modular warehouse management system. HiLIS manages, controls and monitors all material flow processes online and ensures maximum transparency and system availability in all functional areas. Energy optimization with HiLIS Eco-Powermanagement.
The advantages of multi-solution intralogistics systems
- Increased storage capacity and throughput with one overall system through automation - even with different product groups
- Digitalization and acceleration of processes
- Compensating for the shortage of skilled workers
- Just-in-time and just-in-sequence supply of production and order picking
- Consolidation of different warehouses, goods sizes and handling speeds at a few space-saving, ergonomic picking workstations
- A warehouse management system for the entire material flow including Kanban material replenishment
Multi-solution project comprising an automated high-bay warehouse and AutoStore System® for the new logistics center at iDM Energiesysteme GmbH in Matrei
The iDM Group is Austria's largest manufacturer of heating heat pumps. Over 400 employees develop, produce and sell over 10,000 heat pumps for heating, cooling and hot water every year. iDM has made a name for itself with its development expertise and numerous innovations.
The intelligent iDM energy manager "Navigator 2.0" controls the heat pump, uses weather forecasts to adjust heat demand and solar power yields, learns the heating and cooling behaviour of individual rooms and optimizes running times by calling up electricity prices on an hourly basis. In this way, iDM makes a significant contribution to the energy transition with efficient and clean heat for generations.
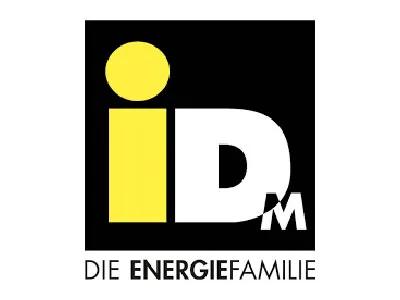
Facts
AutoStore® warehouse | High-bay warehouse |
---|---|
|
|
iDM Energiesysteme GmbH | Matrei, Tyrol | Reference film
Large and small parts handling with HRL, AGV, production connection and AutoStore® system at HASCO
In 85 years, HASCO Hasenclever GmbH und Co. KG has developed from a craft business into a globally successful industrial company that supplies high-precision products for tool and mold making. To keep pace with this growth, they commissioned HÖRMANN Intralogistics to build a high-bay warehouse in Lüdenscheid in 2012, followed by the addition of an AutoStore® system in 2022.
-
The delivered raw panels are transported from the incoming goods area to the cutting line. An AGV driverless transport system distributes the pre-cut panels, which are placed on HASCO pallets, between cutting, high-bay warehouse, processing and dispatch.
-
At the high-bay warehouse, the pallets, stacked up to 3 high, are transferred from the AGV to the conveyor, unstacked and transferred to the storage and retrieval machine (SRM) for storage. During pallet retrieval, the pallets are automatically stacked again and transported via the AGV either for processing or shipping.
-
For the small parts, the dynamic AutoStore® system was subsequently installed at HASCO. Up to 144 storage and 720 retrieval operations per hour can be carried out at four Carousel workstations.
- Warehouse management and control for the entire handling of large and small parts is handled by the tried-and-tested HÖRMANN Intralogistics Warehouse Management System HiLIS, which communicates with the on-site HOST via an SAP interface.
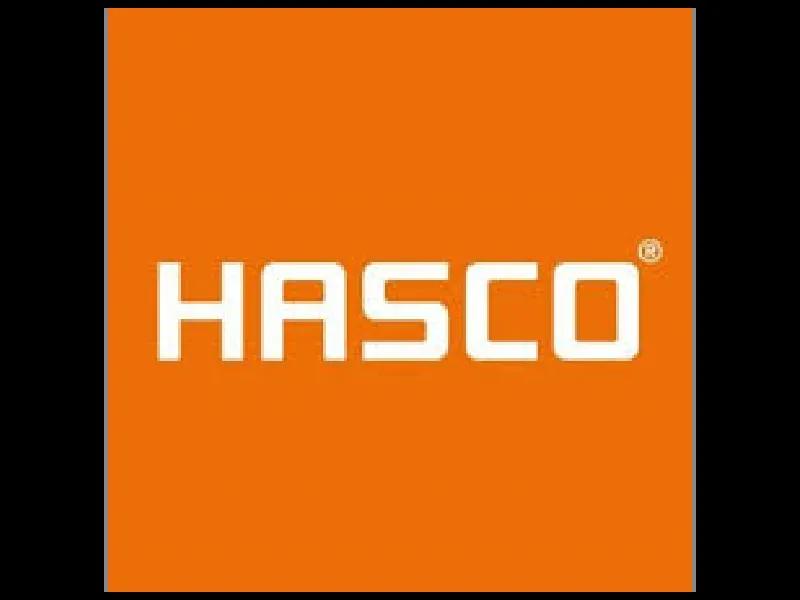
Facts
AutoStore® warehouse | High-bay warehouse |
---|---|
|
|
Fully automated multi-solution storage system at heat pump manufacturer Hoval spol. s r.o. in Slovakia
The renowned international heat pump supplier Hoval spol. s r.o. is increasing its capacities due to high demand with a fully automated storage system consisting of a pallet high-bay warehouse, conveyor technology and AutoStore® small parts warehouse. HÖRMANN Intralogistics was able to convince with its concept and is implementing the system in Slovakia as general contractor.
The plant in Istebnè, SK follows two current trends: On the one hand, HÖRMANN Intralogistics has already received its third order in the trend sector of heat pumps, which is experiencing an enormous upswing due to climate change and environmental protection targets. Secondly, fully automated multi-solution systems are increasingly being built in order to further optimize the degree of automation.
The storage system combines two different systems for large and small parts intralogistics. The centerpiece is a three-aisle pallet high-bay warehouse in silo design.
An Autostore® system is being built parallel to the high-bay warehouse. This offers space for 3,000 containers. The material flow of the complex multi-solution solution is controlled and monitored by the HiLIS Warehouse Management System, which synchronizes the two automated storage areas and optimizes material flows for combined picking workstations.
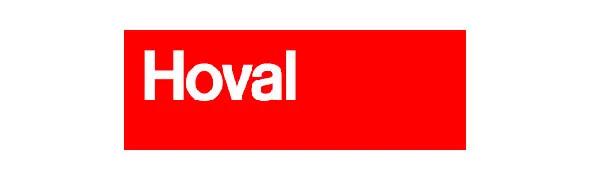
Facts
Pallet- High-bay warehouse |
AutoStore® warehouse |
---|---|
|
|
Analyze your material flow now & get a solution recommendation!
Are you reaching the limits of your manual warehouse in terms of space and personnel requirements? We will take a look at your current and target situation and find a solution. Please feel free to contact us without obligation.