AutoStore® small parts warehouse for IDS Imaging Development Systems in Obersulm
Within little more than 20 years, Imaging Development Systems GmbH has developed from a 2-man company to a worldwide leading manufacturer of digital industrial cameras with about 300 employees. Every year, the company develops and manufactures around 200,000 high-quality cameras "Made in Germany". Subsidiaries in the USA, Japan and the UK, as well as representative offices in Europe and Asia make IDS an international player. Hörmann Logistik realizes a fully automated small parts warehouse in an existing warehouse at their headquarters in Obersulm, in which goods receipts or picking can take place at any workstation at any time. The implementation of the innovative small parts warehouse AutoStore® comes under general contractorship.
Concept
For the customised design of the AutoStore® system, Hörmann Logistik performed, during the planning phase, several system simulations with real data from IDS. The daily operating times of 10 hours, together with other customer requirements and the simulation results, led to a system configuration with approx. 2,610 bins measuring 649 mm x 449 mm x 220 mm (L x W x H) on 10 levels.
5 autonomous robots serve for the supply and disposal of the three Carousel workstations, one of them is assigned for goods receipt, one for goods issue to production and one for goods issue to shipping.. The AutoStore® system consists of an aluminium grid system covered on three sides with a total size of 10.6 m x 11.2 m x 2.4 m (L x W x H), excluding the service platform.
Within the grid, stacks of 10 bins each stand directly on the hall floor. The battery-powered, autonomous robots move on the grid rail system above the bin stacks. They pick up the bins, re-sort them as required and serve them at the carousel ports. The maximum total weight of the bins is 35 kg with a net payload of around 30 kg. A weighing unit at the ports prevents exceeding the maximum weight. Separating inserts in the bins allow flexible use for several articles at the same time.
Four pairs of wheels move the robots in two directions. Their geometry allows them to reach any position in the grid. They communicate via WLAN with the AutoStore control system, which assigns the transport orders to the individual robots. If the order load is low or the battery capacity is too low, the robots drive automatically to one of the charging stations located at the edge of the grid. The AutoStore control is located on the adjacent service platform.
The robots move on the grid with an acceleration of 0.8 m/s² and a speed of 3.1 m/s.
The system is suitable for 800 storage and retrieval operations per day.
HiLIS AS, the warehouse management and control system specially designed for AutoStore®, controls the system. AutoStore® "only" knows the bin number in the system, but not its contents. The higher-level HiLIS AS warehouse management and control system knows the contents of each bin, manages and controls the AutoStore® system and implements all logistical processes including interfaces to the ERP system. The understandable, graphical user interface of HiLIS AS provides clear working and picking instructions via touch screen. In addition, HiLIS AS supports permanent inventory processes, empty bin insertion, status dialogues, special accesses to the bins and much more.
AutoStore® takes over complete picking orders (task group) with all individual picking positions (task). With a lead-time of 30 minutes, AutoStore® with its integrated optimization algorithms ensures maximum efficiency in the processing of orders.
The AutoStore® small parts warehouse at IDS in Obersulm went live in May 2019.
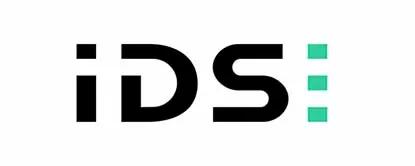