AutoStore® small parts warehouse for the storage of automotive spare parts at BeON in Ettlingen
The BeON GmbH & Co. KG supplies with its BeON Parts Center the Citroen, Peugeot, DS and from 1.10.2020 also Opel partners in southern Germany with repair spare parts.
At the Ettlingen location, an AutoStore® small parts warehouse will be built in an existing logistics property. All workstations will be configured so that goods receipts or order picking can be carried out at any time. Hörmann Logistik has taken over the implementation of the compact and efficient AutoStore® system including the tailor-made warehouse management system HiLIS AS as general contractor.
Concept
For the design of the logistics property, BeON commissioned PROLOG-TEAM Logistics and Organisation Consultancy to develop an optimal overall concept. Based on this concept data Hörmann Logistik carried out several system simulations to determine the perfect AutoStore® system configuration. The individual customer requirements and the simulation results led to a system configuration with initially 8,400 containers (maximum capacity 10,400 containers) measuring 649 mm x 449 mm x 330 mm (L x W x H), 10 robots from the "Red Line" series and 3 carousel workstation modules. Two further Carousel workstation modules are already planned for expansion.
Of the total of 10 autonomous robots, 8 are oriented to the south and 2 to the north. They supply and dispose of the three Carousel workstations. The required 500 - 750 storage operations usually take place from 8 - 13 o'clock. From 8 a.m. to 7 p.m. the AutoStore® system will enable 2,250 retrievals.
The AutoStore® small parts warehouse consists of an aluminium grid system covered on all sides with the overall dimensions of 19.9 m x 13.6 m x 6.5 m (L x W x H). Stacks of 16 bins each are placed in the grid system directly on the hall floor. A single-double-grid rail system is mounted above the stacks of containers, on which the 10 battery-powered, autonomous robots travel. They pick up containers cooperatively, re-sort them as required and serve them at the three carousel ports. The maximum total weight of the containers is 35 kg, with a net payload of around 30 kg. An overweight check is carried out at the ports to ensure the maximum weight is maintained. The containers can be flexibly subdivided by separating inserts for the use of several articles.
High throughput and maximum energy efficiency
The robots move in two directions by means of their four pairs of wheels arranged in a corner and thus reach any position in the grid. They communicate via WLAN with the AutoStore controller, which assigns the transport orders to the individual robots.
If the order load is low or the battery capacity is too low, the robots drive automatically to one of the 10 charging stations located at the edge of the grid. A charging process of 5 hours per day was calculated for each robot. The robots move on the grid with an acceleration of 0.8 m/s² and a speed of 3.1 m/s.
The system is controlled by the HiLIS AS warehouse management system, which was specially designed for AutoStore®. AutoStore® "only" knows the tote number in the system, but not the contents. The higher-level HiLIS AS knows the content of each container, takes over the higher-level administration and control of the AutoStore® system and implements the logistical processes including the interfaces to the ERP system. The comprehensible, graphical user interface of HiLIS AS provides clear working and picking instructions via touch screen. In addition, HiLIS AS supports permanent inventory processes, empty container insertion, status dialogues, special access to the containers and much more.
For the picking of articles, AutoStore® can transfer complete picking orders (task group) with the individual picking positions (task). With its integrated, intelligent algorithms, AutoStore® continuously optimizes processes. This ensures that the time for the complete processing of an order is reduced to a minimum.
The AutoStore® small-parts warehouse at BeON in Ettlingen will be operational by the end of September 2020.
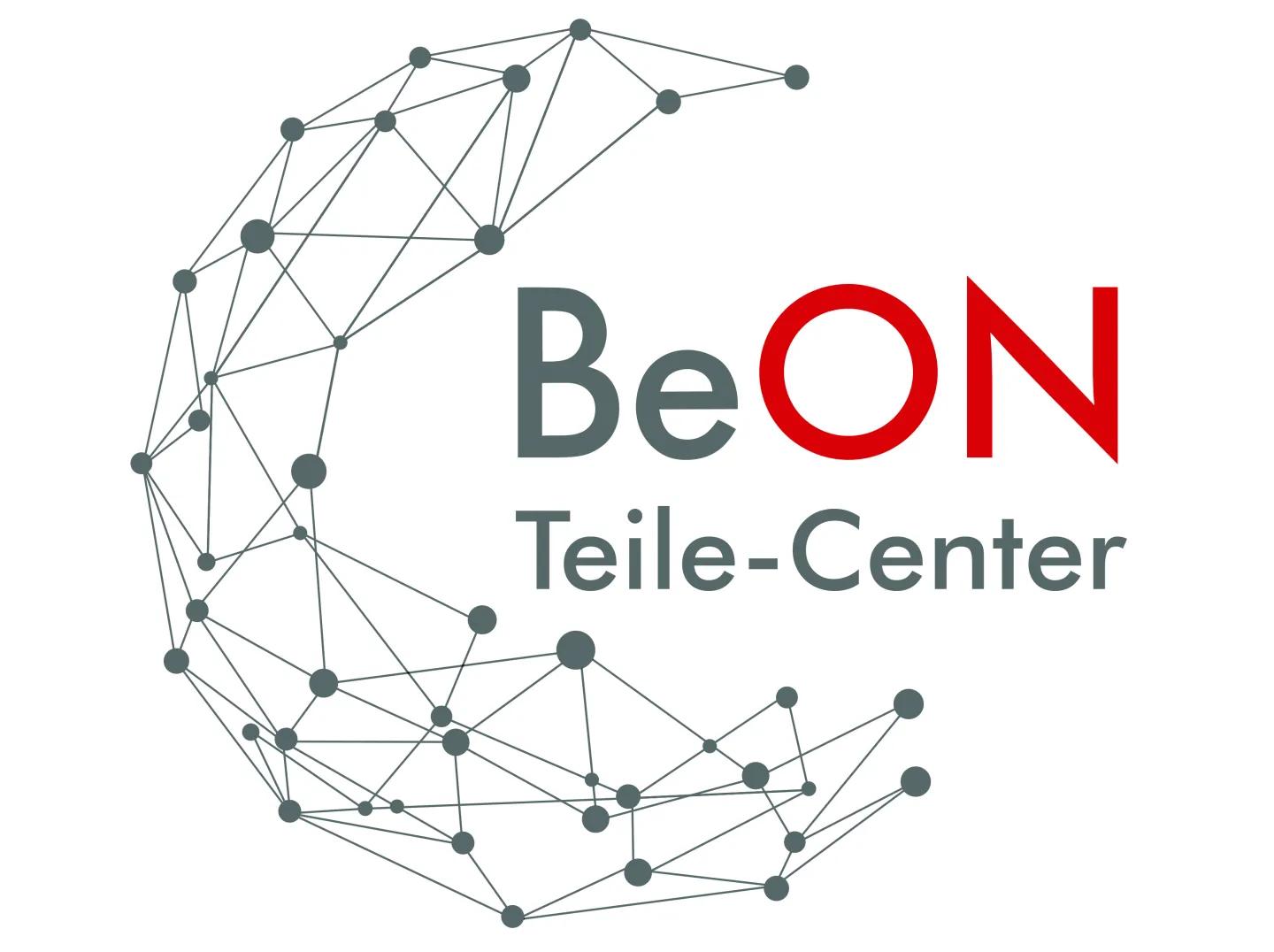