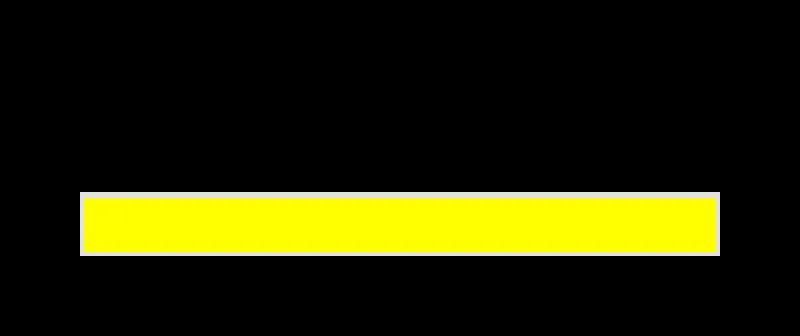
Logistical overall equipment of the new building Kärcher Reparaturzentrum Ahorn
Alfred Kärcher SE & Co.KG offers cleaning systems, cleaning products and services for leisure, household, trade and industry. As an innovation leader, the family-owned company sets standards in technology, service and design that are geared to optimum customer benefits and customer requirements. For the new
Intralogistics project "Logistics Repair Center Ahorn", HÖRMANN Intralogistics has been awarded the contract for the realization of the logistical facilities including the conveyor connections to various functional areas and an automatic miniload for the intermediate storage of products. This includes the connection to the
goods receipt, the transport of various returned packages to the registration workstations, an automatic small parts warehouse, and a connected container conveyor system to repair workstations and shipping.
Goals of the new intralogistics solution at Kärcher's Ahorn repair center
All repair orders from private customers, trade and industry are to converge centrally at the "Ahorn Repair Center" for repair and return to the owner. The new AKL with the connecting conveyor technology is to perform the following functions:
- The throughput time of repair orders is reduced by the automated processes
considerably.
- Employees in the repair center do not have to leave their repair stations, but are supplied there with orders and the corresponding spare parts largely automatically
- The equipment is retrieved according to resources and automatically delivered to the repair stations. promoted
- Not-repairable devices are supplied to the scrapping
- Repaired devices are conveyed directly to packaging and onward to shipping
Customized material flow concept for repair and service centers
In goods receipt, completely heterogeneous parcels delivered by freight forwarders are received without loading aids, almost as "bulk goods" and transported to the collection points by bulk conveying (quantity formation). Since the packages are not temporarily stored in the miniload, the intake capacity of the incoming goods conveyor system was of decisive importance for the allocation. The dimensions of the packages vary from 100 x 100 x 20 mm to 1,200 x 800 x 710 mm with a maximum weight of 50 kg.
In order to ensure maximum system availability despite these varying LE dimensions, HÖRMANN Intralogistics placed great emphasis on perfect guidance of the LE by means of belt conveyors, as well as the avoidance of any interfering edges in its system solution. All transfers, lateral guides and chutes are designed in such a way that snagging can be ruled out.
The supply of the individual capture workstations takes place via one vertical diverter each, which "portions" the packages from the bulk and thus makes them available at the workstations. After sifting/acquisition, the unit is conveyed in an empty container, provided by accumulating roller conveyors, in the direction of the miniload. Used cartons to be disposed of are transported away trouble-free via an individually dimensioned belt conveyor. At the storage loop of the miniload, belt conveyors take over the load units and transfer 2 totes at a time lengthwise to the storage and retrieval system.
The repair units are retrieved from the miniload by the SRM system and fed to the repair workstations via double scaffold chute lifters. From the repair workstations, the repaired units in the totes are preferably conveyed directly to the packing workstations, where they are packed and immediately transported to shipping. The resulting empty containers are automatically conveyed back to the collection workstations. A narrow-aisle warehouse is also manually loaded and unloaded with spare parts and packaging materials on Euro pallets. The Euro pallets (1,200 x 850 mm) can be up to 2.3 m high and weigh 800 kg.
Facts AKL and conveyor technology Kärcher repair center Ahorn:
- 2-aisle AKL 70.9 x 10.8 x 17.6 m (L x W x H) with double-deep longitudinal storage
- 2 miniload AKL stacker cranes
- 20,648 AKL storage locations for equipment and spare parts
- Storage and retrieval capacity each 204 LE / h
- Operating time maximum 2 shifts on 5 days / week
The new intralogistics solution at Kärcher's Ahorn logistics repair center is scheduled for September 2023 to go into operation.
www.hoermann-intralogistics.com, April 2023