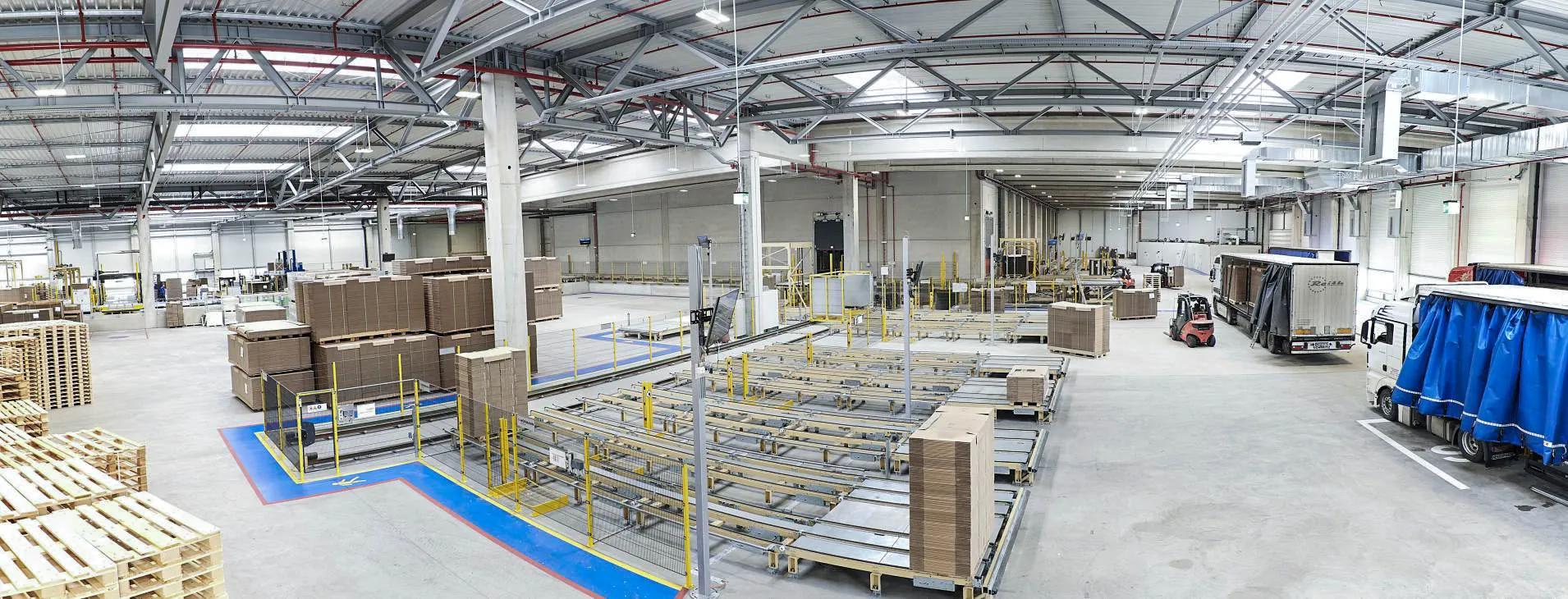
Reference Kunert Corrugated Board
Automatic channel storage for small and large format pallets at Kunert Wellpappe
Kunert Wellpappe Bad Neustadt GmbH & Co.KG is part of the family-run Kunert Group. Today, the Kunert Group employs 1,900 people in 16 plants in Europe and Asia. Annually, the Kunert Group produces 300,000 tons of corrugated board cores, edge protectors and packaging, as well as over 225,000 tons of corrugated board cores. A new automated high-bay warehouse was built at the Bad Neustadt site to create space for production expansions and to meet changing customer requirements for smaller order quantities, shorter delivery cycles and efficient inventory management. With an innovative concept, HÖRMANN Logistik took over the realization of the new warehouse with connecting conveyor technology. Special feature of the four-aisle channel warehouse is the multiple-deep cross storage of a wide variety of finished goods formats on different types of pallets as well as on several sub-pallets.
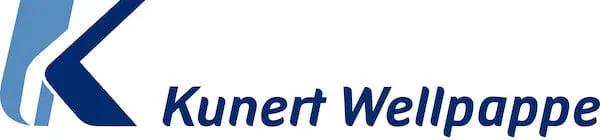
Concept
The packing units are transported from production by a distribution trolley for transfer to the new conveyor system. Already in production, care is taken to ensure that, if possible, two identical packing units are always transported one behind the other, which can then be conveyed as pairs in the high-bay warehouse area and stored and retrieved. This significantly increases the throughput of the warehouse. A packing unit can have up to six sub-pallets. The packing units are centered and checked for length, width, height, pallet width, pallet length and weight via a contour control system.
The conveyor system then brings the packing units to the prezone of the high-bay warehouse, where a pallet circuit with special chain conveyors and roller lifting tables connects the production, high-bay warehouse and shipping preparation areas. For storage in the new channel warehouse, the packing units are precisely positioned at the storage spur with the aid of a light grid. The two-mast storage and retrieval machines (SRMs) are equipped with chain conveyors and channel trucks. In two aisles of the warehouse, the SRMs operate with one channel truck each, while in the other two aisles they operate with two channel trucks each to handle the transport of large pallets.
The channel trucks are battery-powered and are charged on the fly at the AS/RS. The stacker crane picks up the packing unit crosswise and stores it multiple depths in the storage channels with the help of the channel trucks. During order-related retrieval, the HiLIS warehouse management and control system receives a retrieval order via interface from the on-site HOST. The goods are retrieved by the stacker cranes and transported via conveyor technology towards the shipping area. There are different loading areas for truck rear loading and truck side loading.
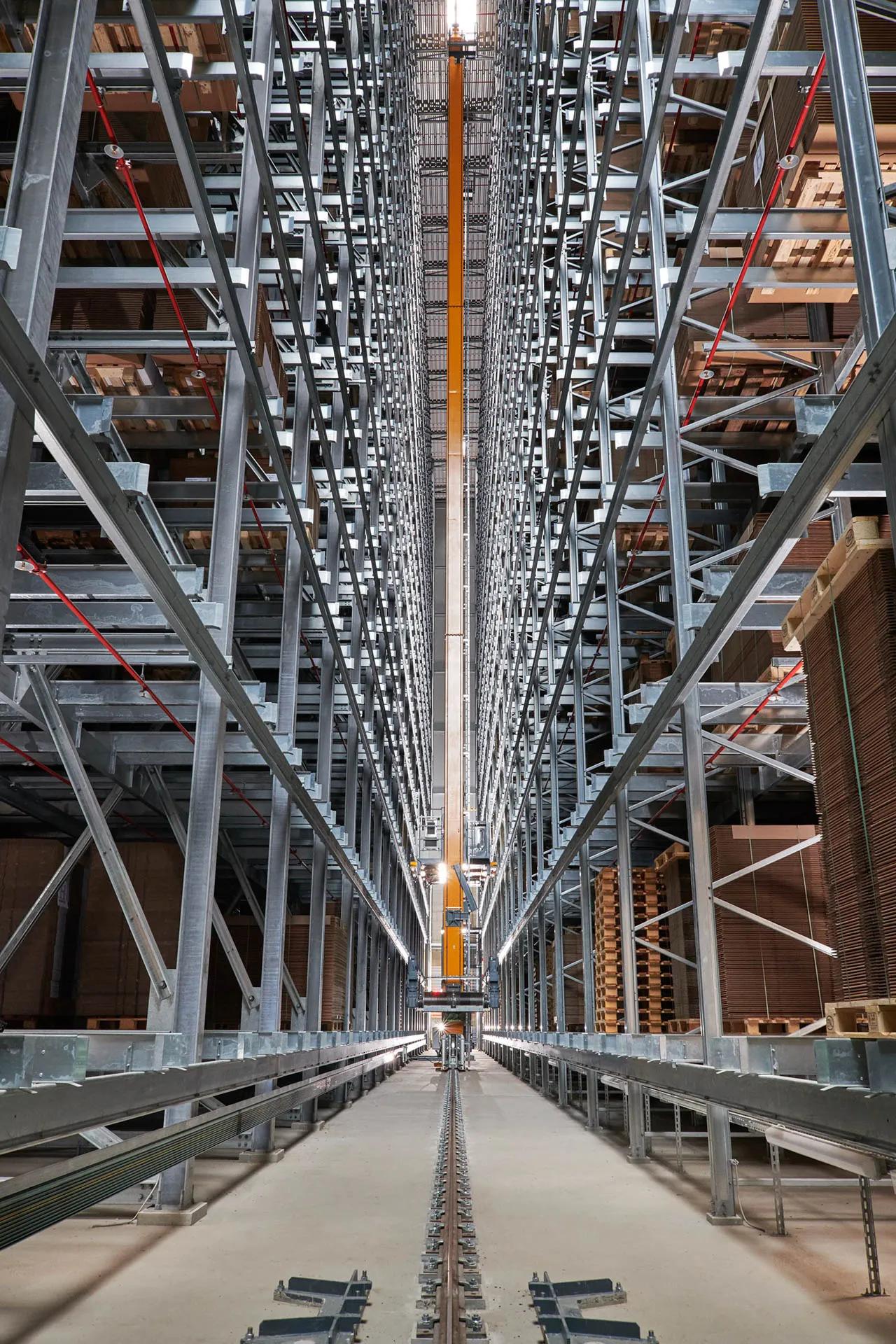
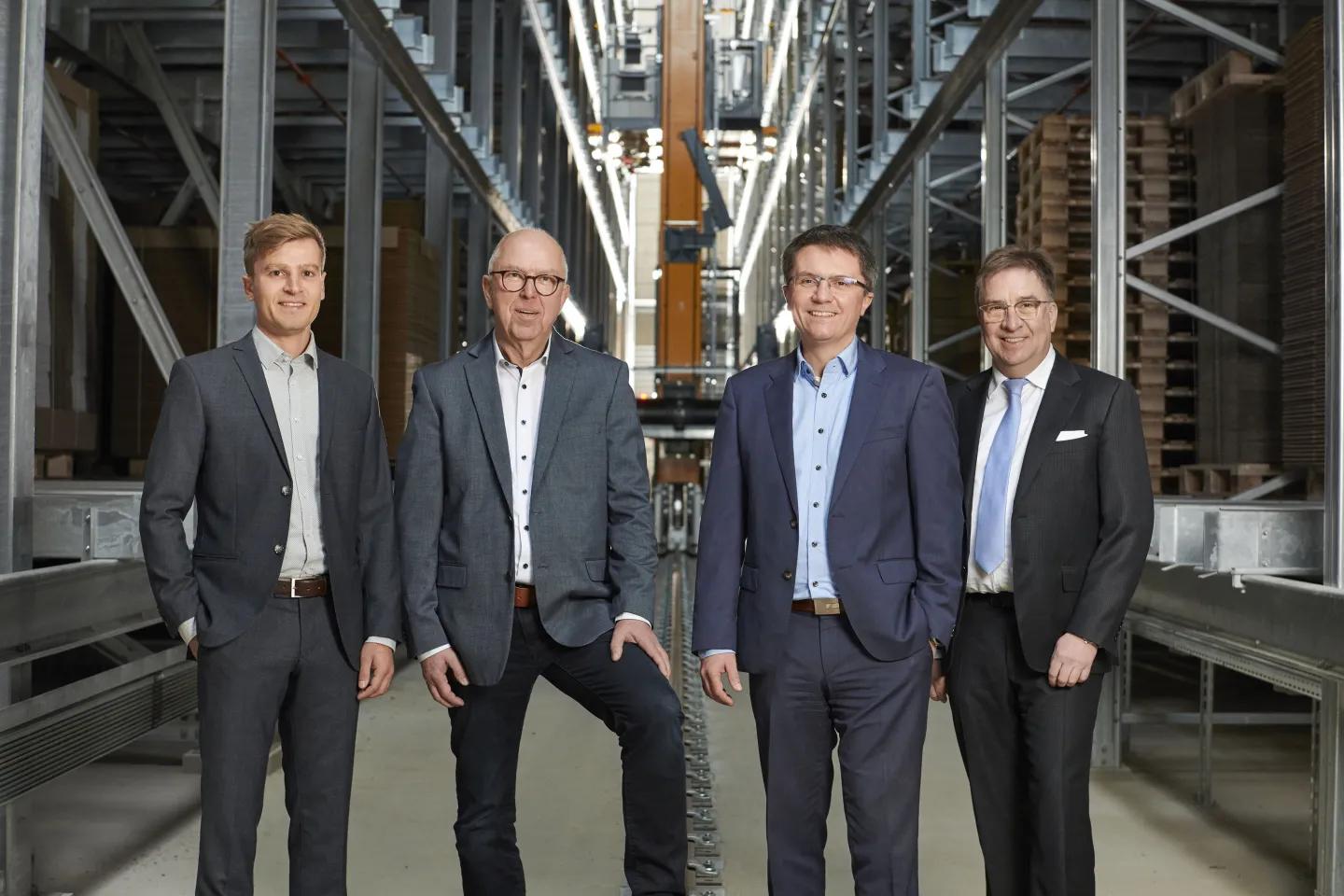
Sophisticated strategies for storage and transport of a wide variety of packaging units
The particular challenge in the detailed planning and realization of the new channel warehouse at Kunert Wellpappe lies in the very different formats as well as the large-format packing units with several sub-pallets. In addition to the transport of these very different packing units on a special conveyor system, a sophisticated compartment detail was required, which makes it possible to use the large compartments in a very flexible and volume-optimized way. The construction height of the high-bay warehouse of approx. 42 m is also unusual.
Highlights
- 4-aisle high-bay warehouse in silo design with multiple-deep storage
- Dimensions: 84 x 46 x 42 m (L x W x H)
- 19,000 pallet spaces
- 2 aisles for max. load dimensions 2,300 x 2,600 x 2,200 mm (L x W x H)
- 2 aisles for large formats with up to 6 euro sub-pallets 3,000 x 2,600 x 2,200 mm (L x W x H)
- High dynamics due to anti-pendulum travel curve control and camera positioning
- Input capacity: 160 pallets / h
- Outfeed capacity: 190 pallets / h
- HiLIS Warehouse Management System
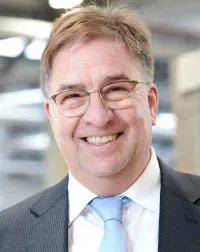
Tailored to our individual requirements, HiLIS, the Warehouse Management System from HÖRMANN Logistik, guarantees maximum flexibility and transparency.
Mathias Kunert
Partner and Managing Director, Kunert Wellpappe Bad Neustadt GmbH