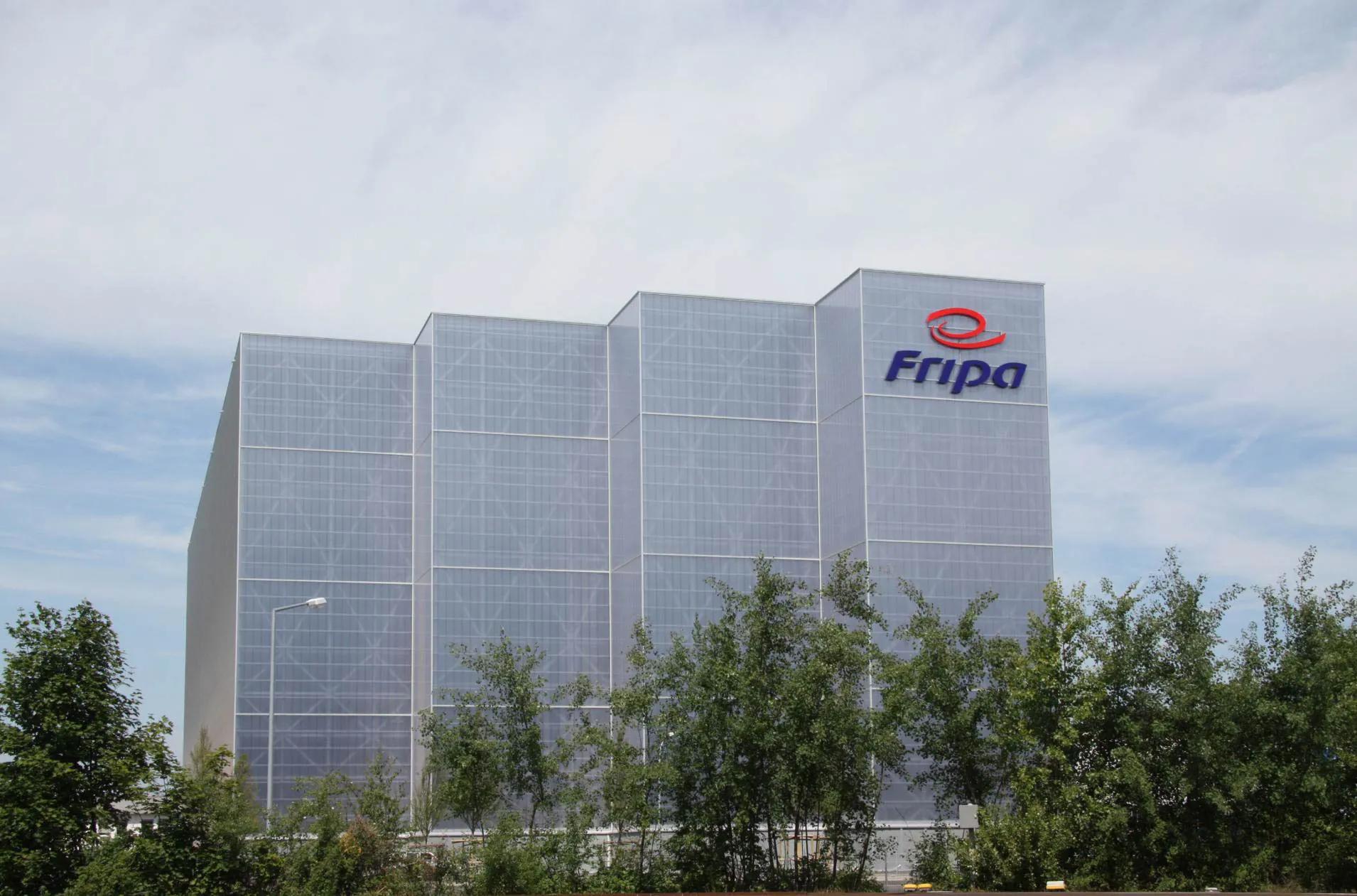
Reference Versandmanufaktur
Caja Robotics revolutionizes the fulfillment of Versandmanufaktur GmbH
The Fripa Papierfabrik Albert Friedrich KG is an internationally sought-after supplier of high-quality hygiene papers. The Miltenberg production site, with approximately 370 employees and several converting lines, is the company's state-of-the-art performance center. The steadily growing sales volumes required a new concept of warehouse logistics, in which the existing three-aisle high-bay warehouse and the block warehouse should be integrated.
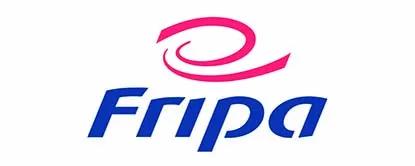
Based on Fripa's requirements, the specialist planning company Luy & Partner GbR developed an overall logistics concept in which the new warehouse management software to be implemented plays a decisive role. In competition with other suppliers, HÖRMANN Logistik was able to prevail as general contractor for the overall project. The warehouse management system HiLIS fulfills all specifications for a continuous IT and control concept from the production connection to the new high-bay warehouse 2 to be built, the integration of the existing warehouses to the new dispatch.
Concept
The new construction of the four-aisle fully automated high-bay warehouse is designed for four-deep pallet storage of finished goods on Euro pallets. For the most efficient storage and retrieval performance, the storage and retrieval machines (SRMs) were equipped with a special telescopic fork that can pick up to two pallets at a time. The pairing of similar items takes place directly at the infeed points of the new high-bay warehouse. The conveyor connection takes place on two conveyor levels. In the preliminary zone of the HRL 2, a highly dynamic electric monorail takes over the pallet transport.
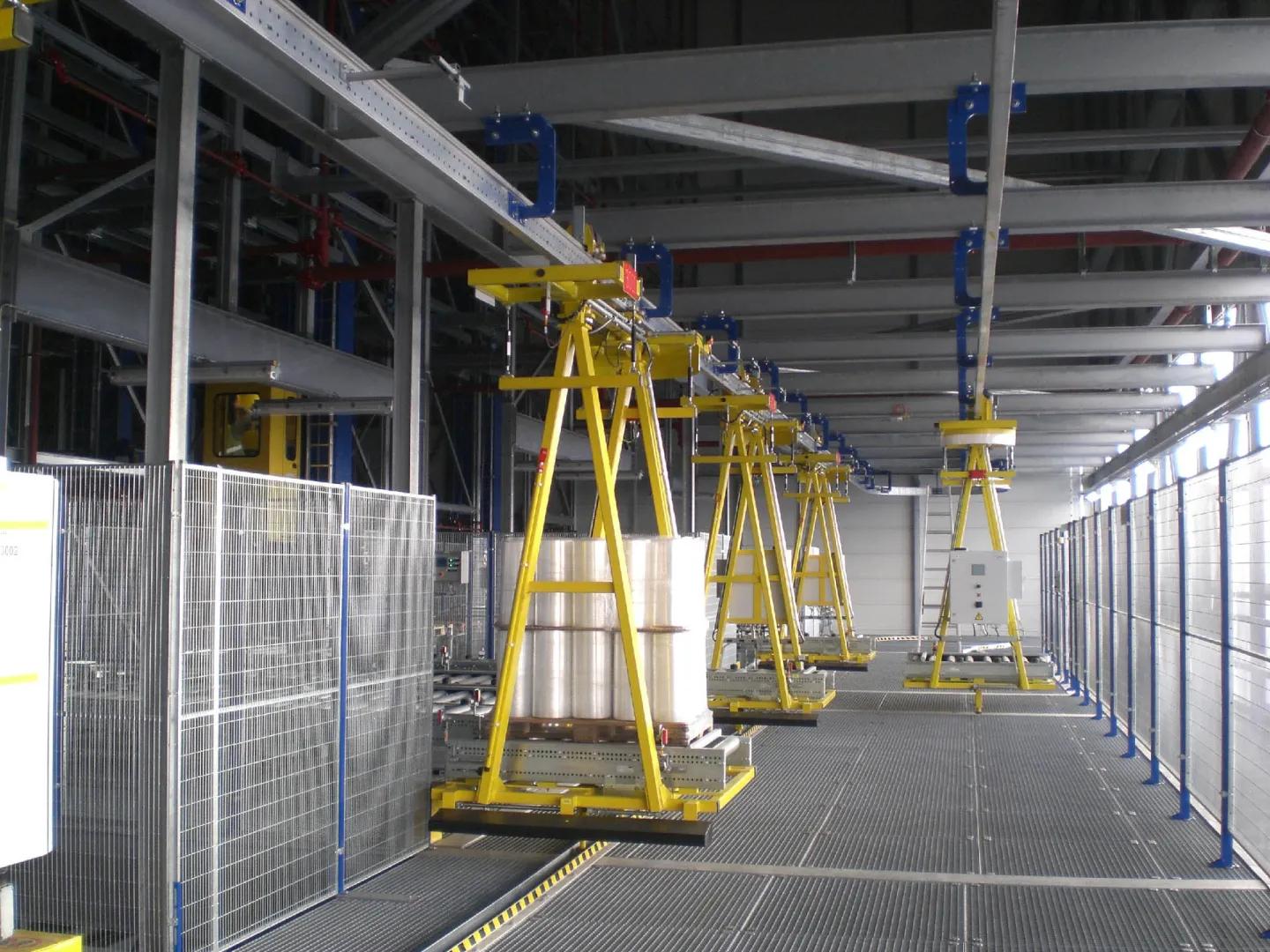
Transport to shipping takes place via vertical conveyors, continuous conveyors and distribution carriages until transfer to one of the 24 gravity roller conveyors. Three gravity roller conveyors are assigned to each loading gate. Shipping displays, which are controlled by HiLIS, show the shipper the required loading information. As a special feature, a photo is automatically taken of each truck load and stored in the warehouse management system. The two-mast design stacker cranes are equipped with the HiLIS Eco-Power Management System, which saves up to 25% of energy consumption through intelligent energy balancing.
After commissioning the new high-bay warehouse, HÖRMANN Logistik subjected the existing high-bay warehouse to a complete retrofit. In addition to mechanical adjustments to the existing storage and retrieval machines and conveyor technology, these were equipped with new control technology and integrated into the HiLIS WMS. The existing high-bay warehouse is connected to the new building via a conveyor technology bridge.
Highlights
- Four-aisle high-bay warehouse
- 4 stacker cranes in two-mast design with special telescopic forks
- Four-aisle deep storage
- Pair transport
- 210 / 200 pallets/h storage or retrieval capacity
- 21,500 pallet locations
- Retrofit three-aisle high-bay channel warehouse with 3 stacker cranes
- 6,500 storage locations
- Implementation HiLIS WMS
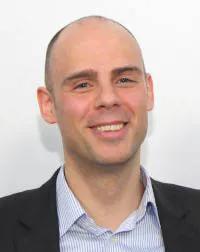
With the best references and a convincing and consistent IT concept, HÖRMANN Logistik was able to convince us in the selection of suppliers for our demanding project. The high expectations for the new high-bay warehouse construction, the modernization and the integration of the existing high-bay warehouse were excellently met by HÖRMANN Logistik as general contractor.
Jochen Giegerich
Purchasing Manager Technology, Fripa Papierfabrik
Albert Friedrich KG