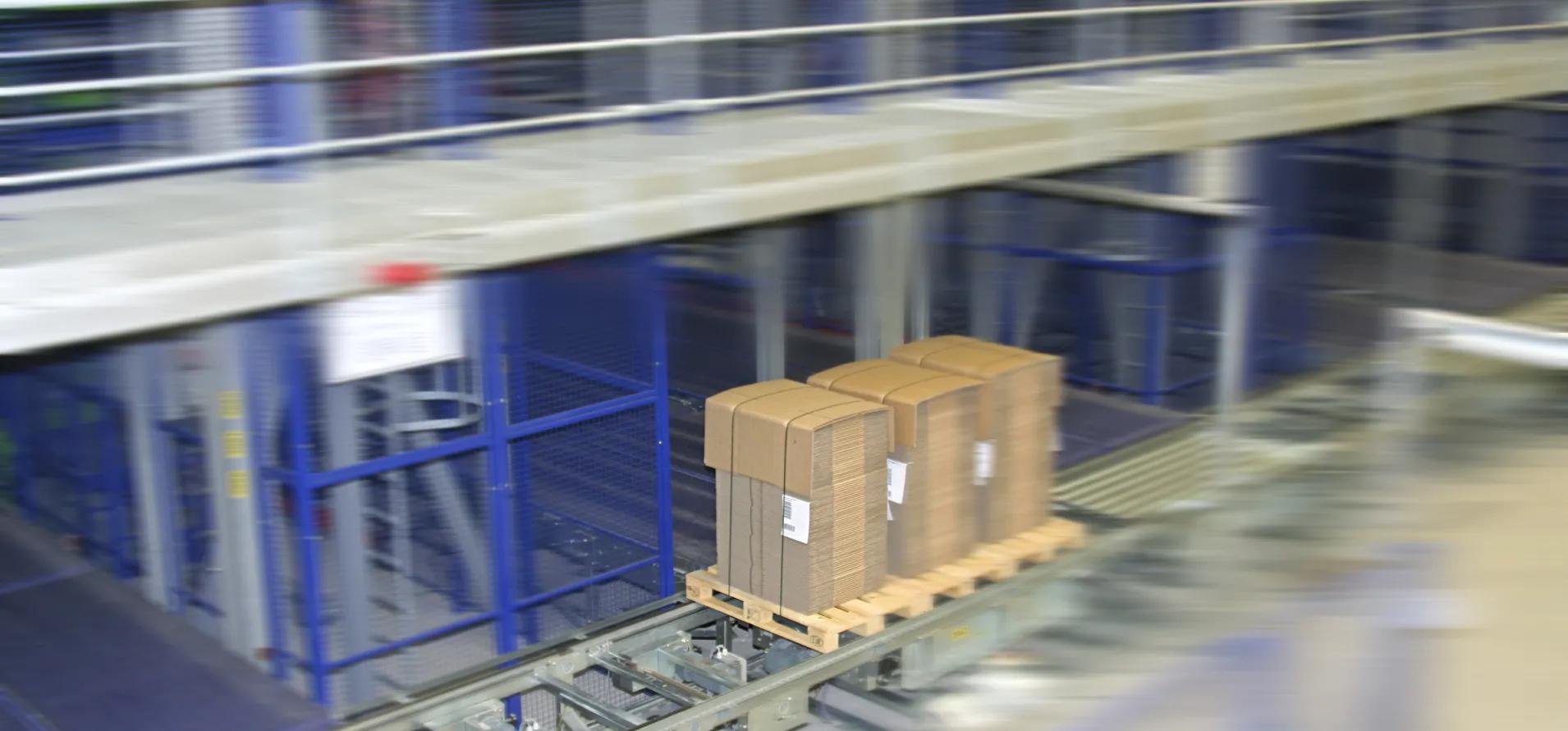
Accessibility Reinforcement Act
Declaration of accessibility
HÖRMANN Intralogistics Solutions GmbH endeavors to make its website https://www.hoermann-intralogistics.com in accordance with the Bavarian Act on Equality, Integration and Participation of Persons with Disabilities (Bayerisches Behindertengleichstellungsgesetz - BayBGG) and the Bavarian Barrier-free Information Technology Ordinance (BayBITV) for the implementation of Directive (EU) 2019/882 of the European Parliament and of the Council (‘European Accessibility Act’ (EAA)).
This accessibility statement applies to the currently published version of the website https://www.hoermann-intralogistics.com.
Status of compliance with requirements
The accessibility requirements are based on the Bavarian Act on Equality, Integration and Participation of Persons with Disabilities (Bayerisches Behindertengleichstellungsgesetz - BayBGG) and the Bavarian Accessible Information Technology Ordinance (BayBITV)
The verification of compliance with the requirements is based on a review carried out in the period from June 1 to June 27, 2025. the compliance check is based on an analysis carried out between 1 and 27 June 2025 using the software tool Accessible Web RAMP.
For the check, all content pages were analyzed by the software tool and the errors were corrected as far as possible. The results are documented in a test report.
Formal confirmation of the accessibility of our website
We have the following formal confirmation of the accessibility of our website: Based on WCAG 2.2 at conformance level "AA" according to the report named above. The last review here took place on 05.06.2025.
Incompatibilities
The existing known incompatibilities are listed below:
1. Non-accessible content
1.1 Text alternatives for graphic page elements
- Linked images and graphic buttons sometimes have no text alternative or this is not equivalent.
- Unlinked, information-bearing images and multimedia objects do not always have an equivalent text alternative.
1.2 Semantic structuring and adaptability
- Subheadings are not always marked up using HTML structural elements.
- The labels "Salutation" and "Postcode" in the contact form are not correctly linked to the associated form field.
- In some cases - such as error handling in the contact form - reference is made exclusively to sensory features such as color and positioning. These references are not comprehensible without the perception of sensory characteristics.
1.3 Distinctness
- Fonts and colors are used on the website in elements that do not have sufficient contrast to the respective background.
- To mitigate this incompatibility, a high-contrast switch has been added to the page frame of this website, which improves the distinctiveness of this content.
- The browser zoom is supported by the website, but when using the text zoom or when enlarging fonts, overlays occur. some parts of the page overlap or are cut off.
- In the case of very small displays, e.g. a display width of 320px, individual content on the website is cut off.
- The flyout menu of a menu item in the main navigation only closes when the hover state of the mouse is changed, but it does not close when the keyboard focus is changed.
1.4 Keyboard operation
- The website can only be operated with the keyboard to a limited extent.
- The current keyboard focus is not visible. Some controls such as the jump marker to the top of the page, the scroll function of the teaser slider on the homepage and the entire mobile menu cannot be reached or operated using the keyboard.
1.5 Time limits and moving content
- The teaser slider on the homepage automatically switches between different content. This movement neither stops automatically nor can it be stopped manually.
1.6 Readability
- The website is currently offered in German.
Non-German words, e.g. technical terms, are not marked.
1.7 Other
- The HTML of the website is not valid.
- PDFs available for download, such as flyers, are not accessible.
- Content is not yet provided in plain language or sign language.
The offers that are currently not fully accessible will be successively adapted accordingly.
2. Disproportionate burden
The exception due to disproportionate burden according to Art. 5 of Directive (EU) 2016/2102 is temporarily invoked here.
- Subtitles for videos have not yet been fully maintained or automatically created in some cases (WCAG success criterion 1.2.2).
- No audio description is provided for videos that require an audio description (WCAG success criterion 1.2.3).
- Integrated, external third-party content, for example videos, podcasts or posts from social media platforms are not fully accessible.
Creation of this accessibility statement
This statement was created on 25.06.2025.
Feedback and contact details
Would you like to inform us of any existing barriers or request non-accessible content in an accessible format? Please contact our responsible contact persons.
Responsible for barrier-free accessibility and the processing of messages received as part of the feedback mechanism is:
HÖRMANN Intralogistics Solutions GmbH
Gneisenaustraße 15
80992 Munich
https://www.hoermann-intralogistics.com/de/kontakt
Enforcement procedure
If no satisfactory solution has been found even after your feedback to the above-mentioned contact, you can contact the Barrier-free Information Technology Enforcement and Monitoring Body. After a period of six weeks, you have the right to contact the enforcement and monitoring body directly. With the involvement of all parties concerned, the enforcement body will attempt to determine the circumstances of the lack of accessibility so that the institution can rectify them.
Landesamt für Digitalisierung, Breitband und Vermessung
IT-Dienstleistungszentrum des Freistaats Bayern
St.-Martin-Straße 47
81541 München
E-Mail: bitv@bayern.de
Website: www.ldbv.bayern.de/digitalisierung/bitv.html
Reference Hoval
Fully automated storage system for heat pump production in Istebné
Hoval is one of the leading international companies for heating and indoor climate solutions. In order to meet the enormous demand for heat pumps, they are expanding their production capacities in Slovakia with the highest level of automation
A state-of-the-art automation solution ensures the flow of stock and materials in heat pump production at Hoval's Slovakian site in Istebné. The intelligent combination of two asynchronous storage areas is a stand.-out customization: A pallet high-bay warehouse for large parts and an AutoStore system for small parts. Both systems are brought together at a combined picking workstation and controlled centrally via the HiLIS Warehouse Management System (WMS) - for seamless, consistent and efficient intralogistics.
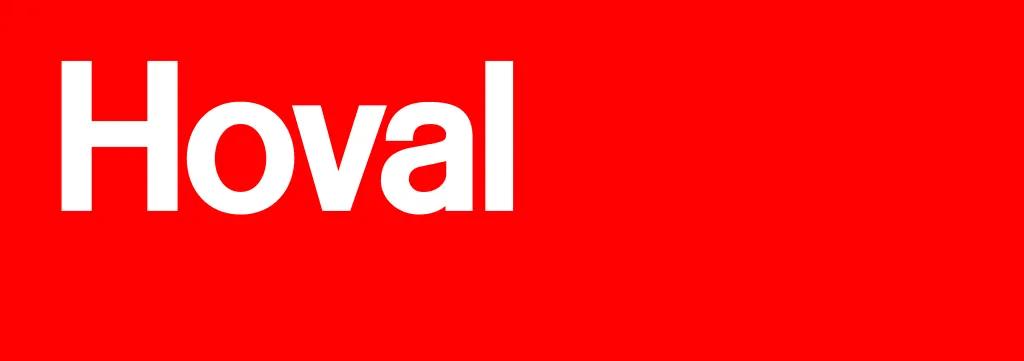
Behind the scenes: The construction stages of the Hoval HRL & Autostore in Istebne, Slovakia
Etap budowy 1: Autostore
Etap budowy 2: HRL
Etap budowy 3a) Jednostka magazynowania i pobierania
Etap budowy 3b) Technologia przenośników
Etap budowy 4: Uruchomienie PLC i HiLIS
Etap budowy 5: Odbiór całego systemu
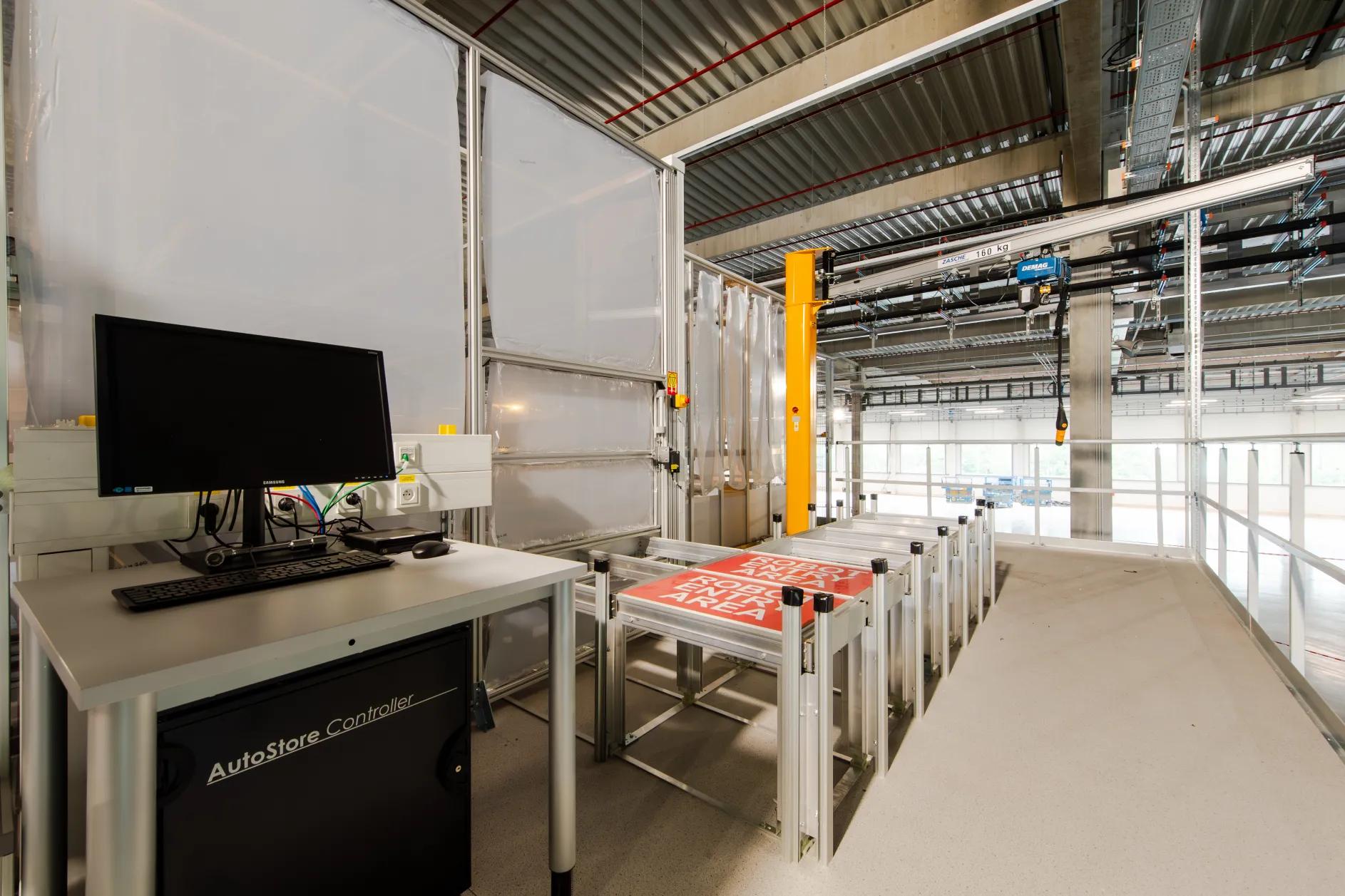
Stage 1: AutoStore
AutoStore, LVS/HiLIS IBN
Installation of the AutoStore® system including WMS HiLIS - subsequent connection to HBW, production and conveyor technology taken into account.
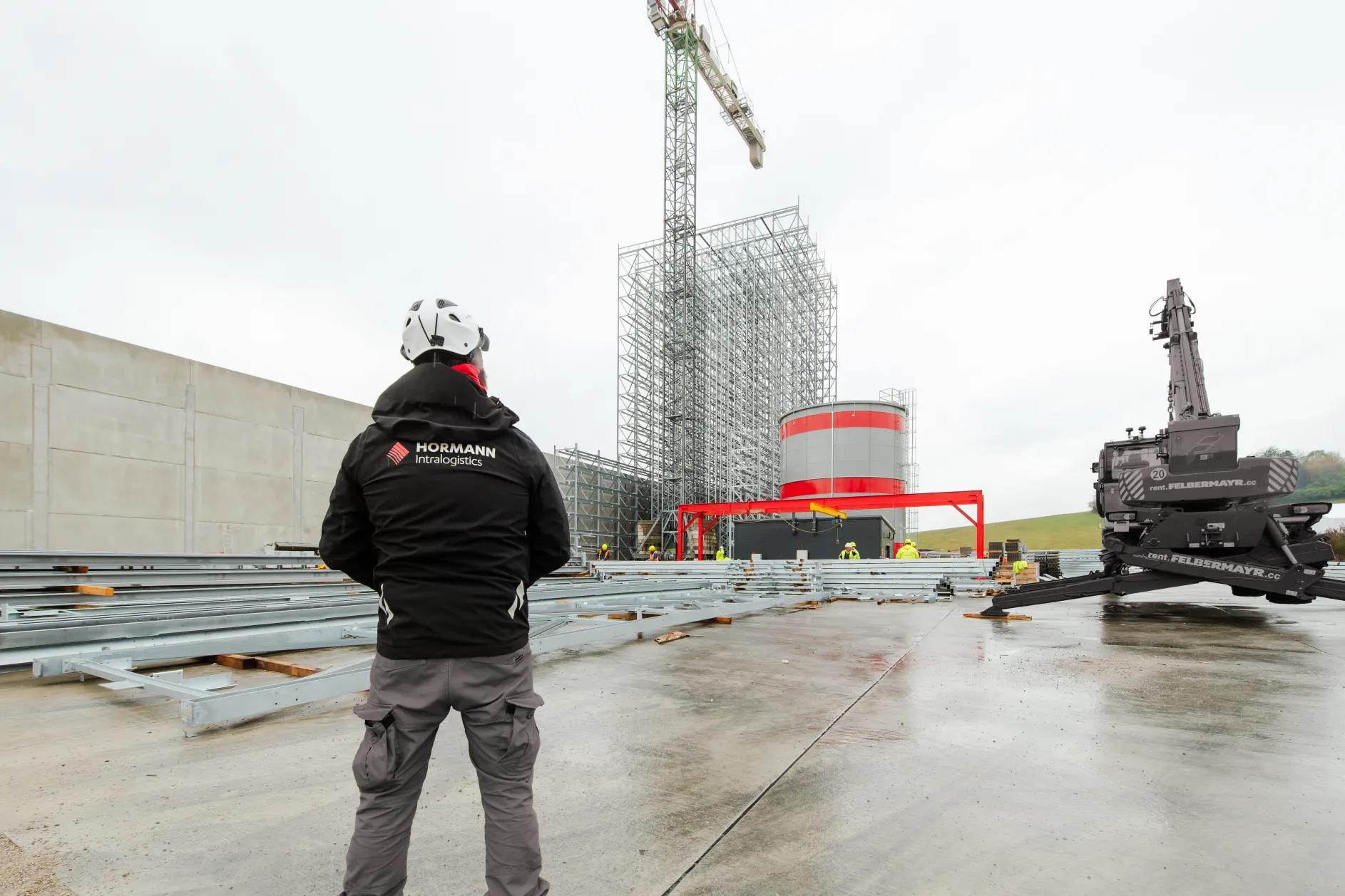
Construction stage 2: HRL
Shelf steel construction, roof + wall, sprinklers
Construction of the shelf steel construction with roof/wall cladding and sprinkler system for the 3-aisle high-bay warehouse
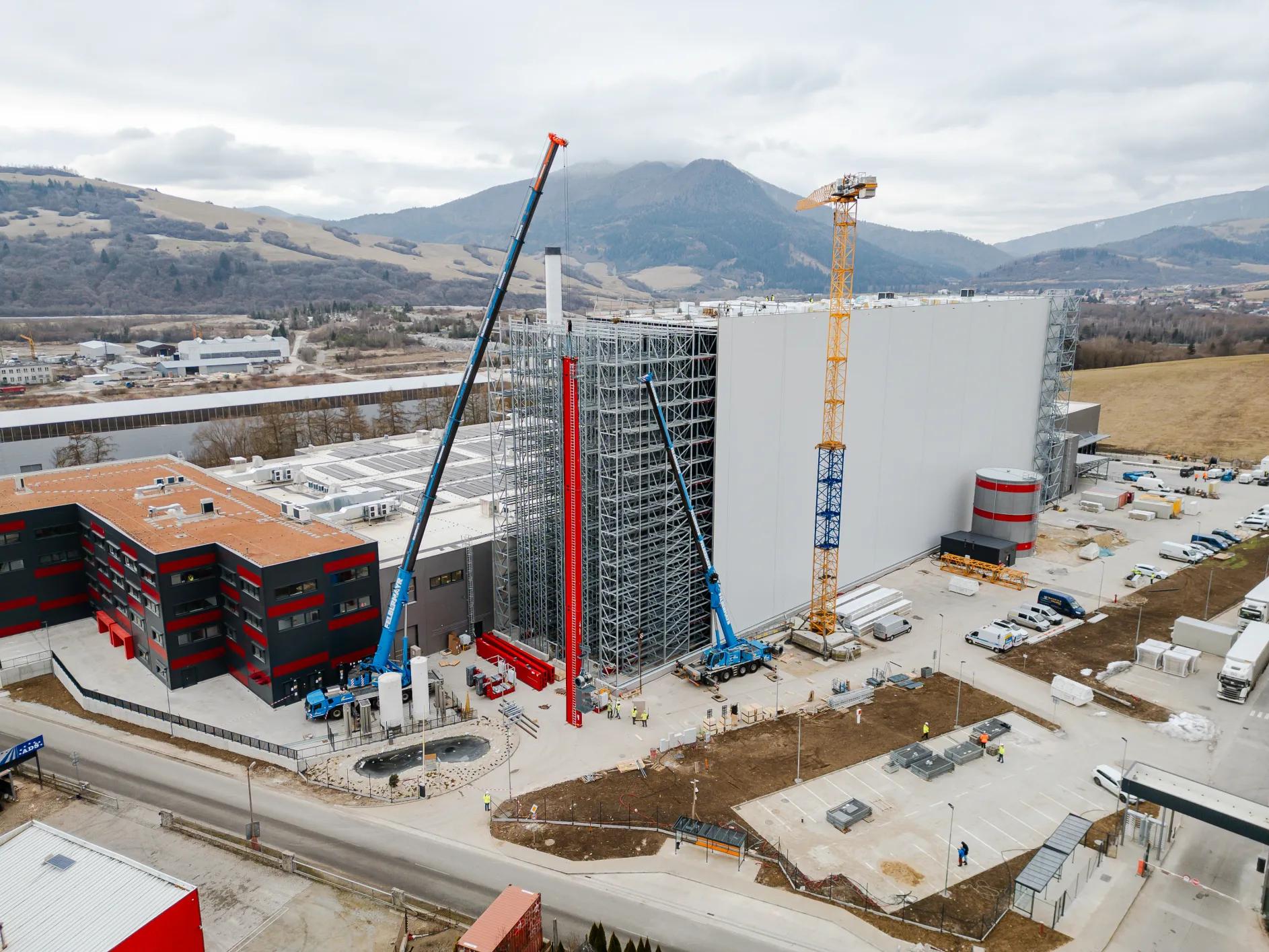
Construction stage 3a) Storage and retrieval unit
Installation and assembly of the storage and retrieval units. Hörmann site management synchronizes different suppliers & trades
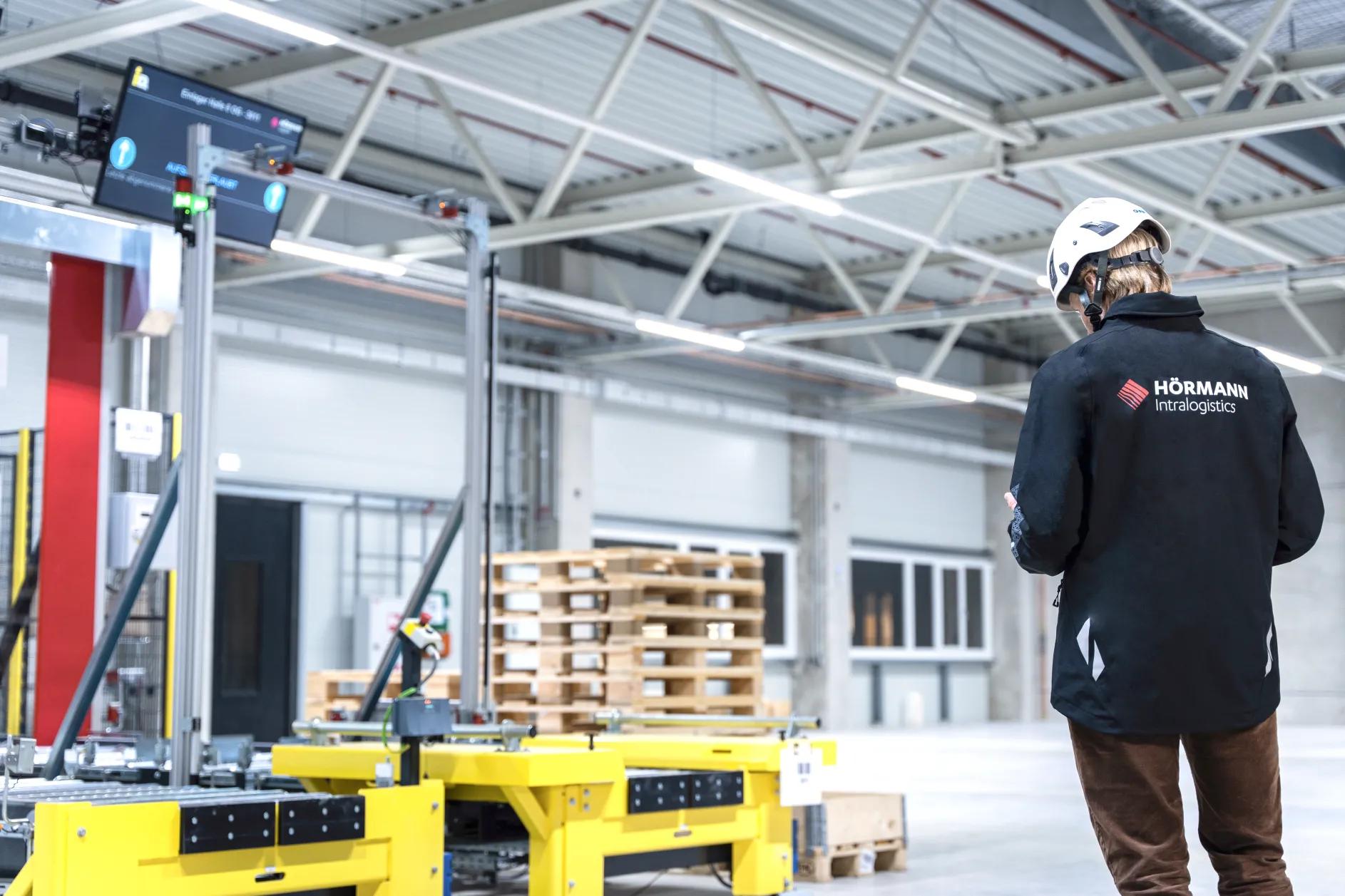
Construction stage 3b) Conveyor technology
Installation of the conveyor technology with all components and connection to the HBW, AutoStore and picking workstations.
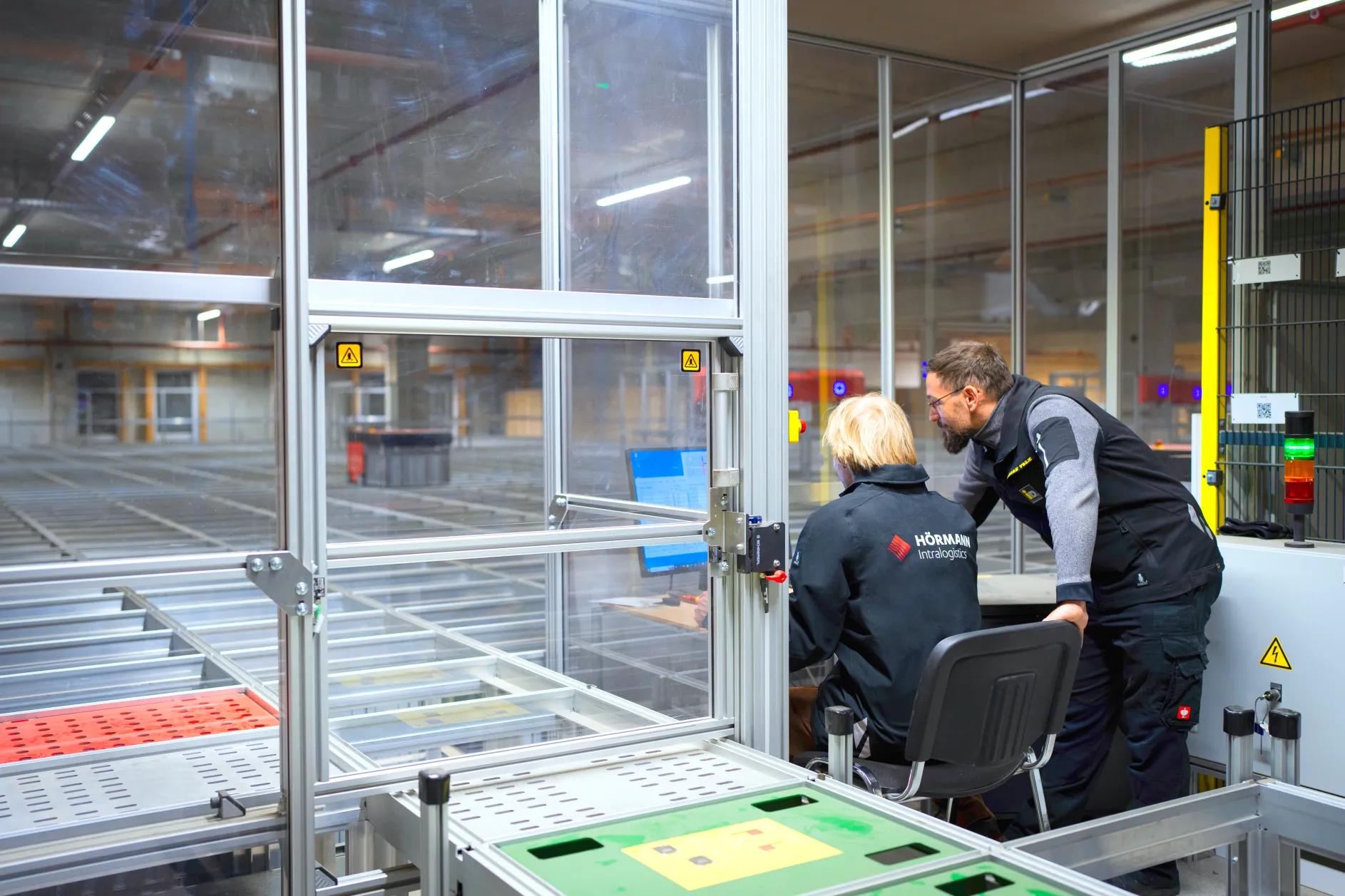
Stage 4: PLC & HiLIS commissioning
Activation of the system by WMS and system control. Drive elements are checked, addressing is set up via PLC, automatic operation is started. The intelligent WMS HiLIS manages the interaction of all components.
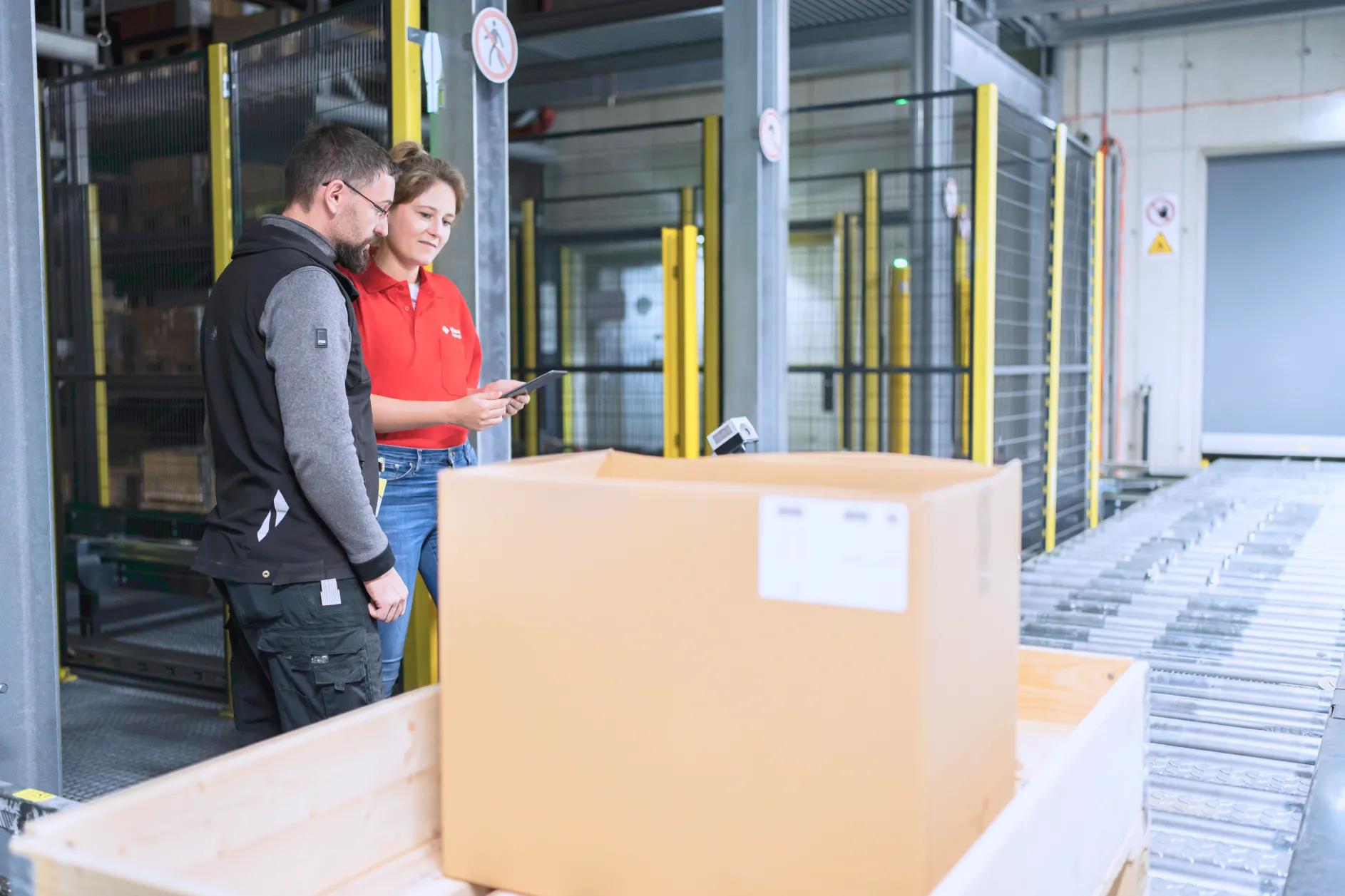
Stage 5: Handover
Training, performance tests, SOP, ramp-up phase, availability test, handover
During the handover, the system is ramped up, key performance indicators are checked and tests are carried out. Employee training concludes the commissioning process. After handover, HÖRMANN Intralogistics customer service is available 24/7.
The concept
High-bay warehouse for pallets
The three-aisle high-bay warehouse in silo design is the backbone of the large parts logistics operations. With a length of 115 m, a width of 22 m and a height of 40 m, it offers space for a large number of pallets. It is equipped with three storage and retrieval machines, each with double-deep telescopic forks. A special feature is the use of extra-wide system pallets, which serve as carriers for finished goods.
The pallet conveyor technology connects various functional areas - from incoming goods and central order picking to outgoing goods and dispatch. The maximum throughput rate is around 100 pallets per hour.
AutoStore for small parts
An AutoStore system for small parts logistics was installed in parallel. The compact cube storage system covers around 85 m² and offers space for around 3,000 containers. Storage and retrieval is fully automated using three "Red Line" robots working at three conveyor ports. The system is supplemented by a service platform with overhead crane and electric chain hoist for ergonomic picking workflows.
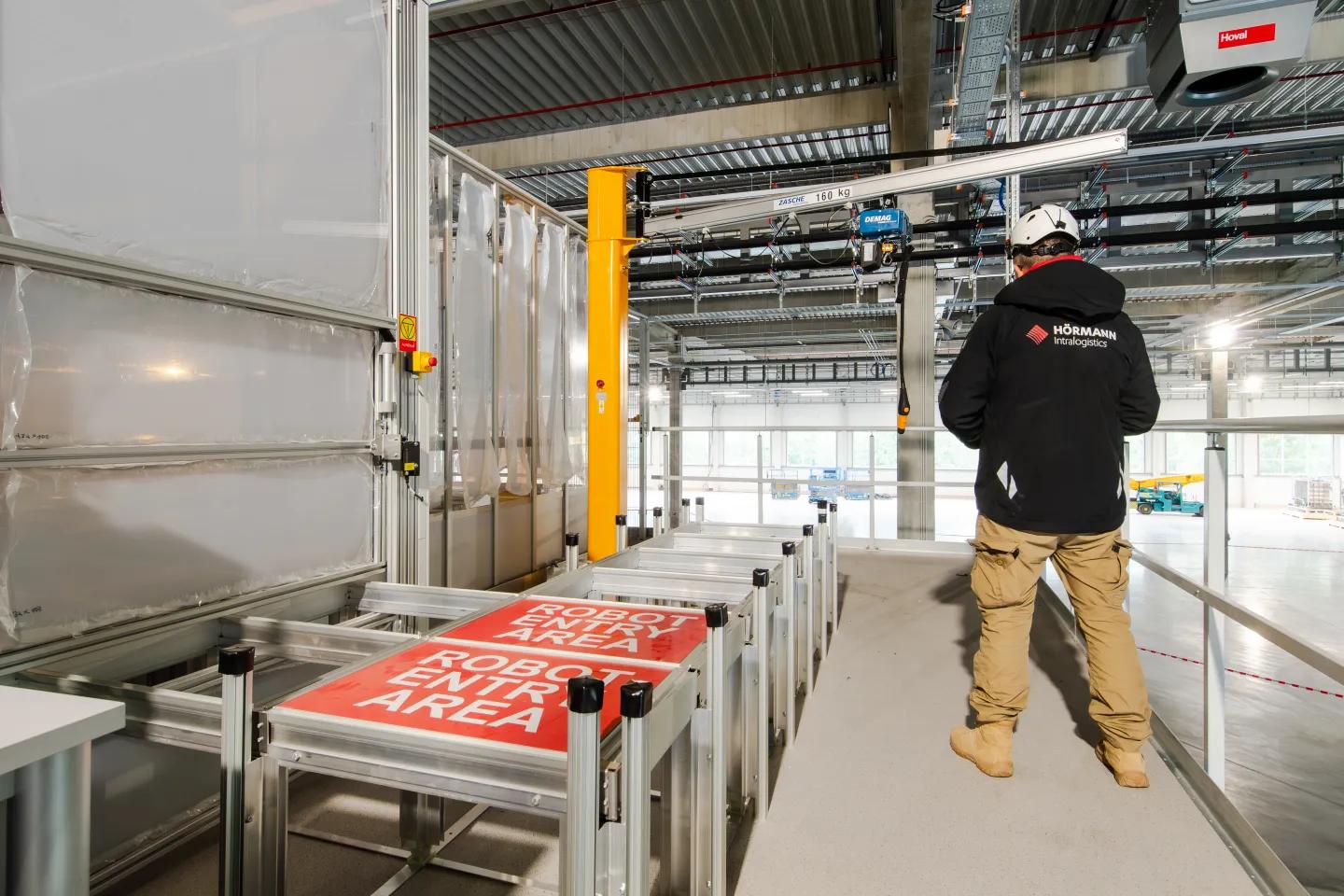
Objectives and challenges of the project:
- Increasing warehouse capacity to meet growing demand in the heat pump segment
- Connecting two asynchronous warehouse areas in a continuous material flow
- Optimizing order picking through combined workstations
- Reducing manual processes through robotics and conveyor technology
- Central control via the HiLIS Warehouse Management System
- Integration into existing production processes during ongoing operations
Facts & Figures
AutoStore® warehouse | High-bay warehouse |
---|---|
|
|
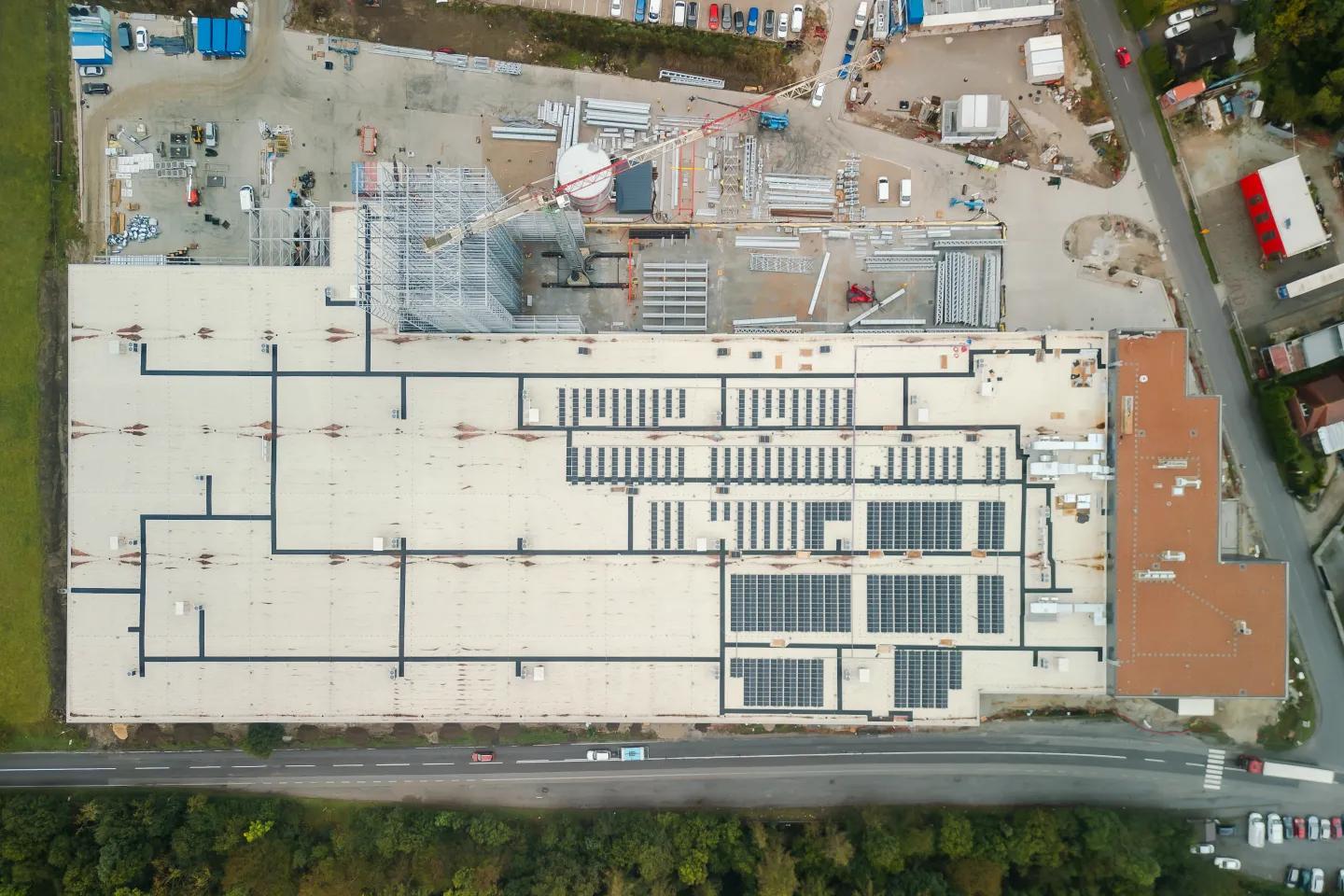
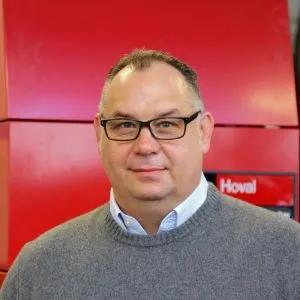
"HÖRMANN Intralogistics impressed us with an all-in package for the future-oriented project in Istebné. We are happy to increase our capacities in the heat pump market with an established and tech-savvy partner."
Dr. Vadim Tcharnetsky
Head of Indirect Procurement, Hoval Group
Picture gallery
Contact us
Do you see yourself in the Hoval story with challenges and possible solutions for your own business? Feel free to contact our project planning experts for a chat. We will give you an assessment of your current and optimized material flow, automation options and an initial target price.