HÖRMANN Logistik GmbH
Imagefilm | 2020 in 70s
Innovation Champion "Top Innovator 2020"! | german
We deliver security in times of Corona | german
Imagefilm 2015
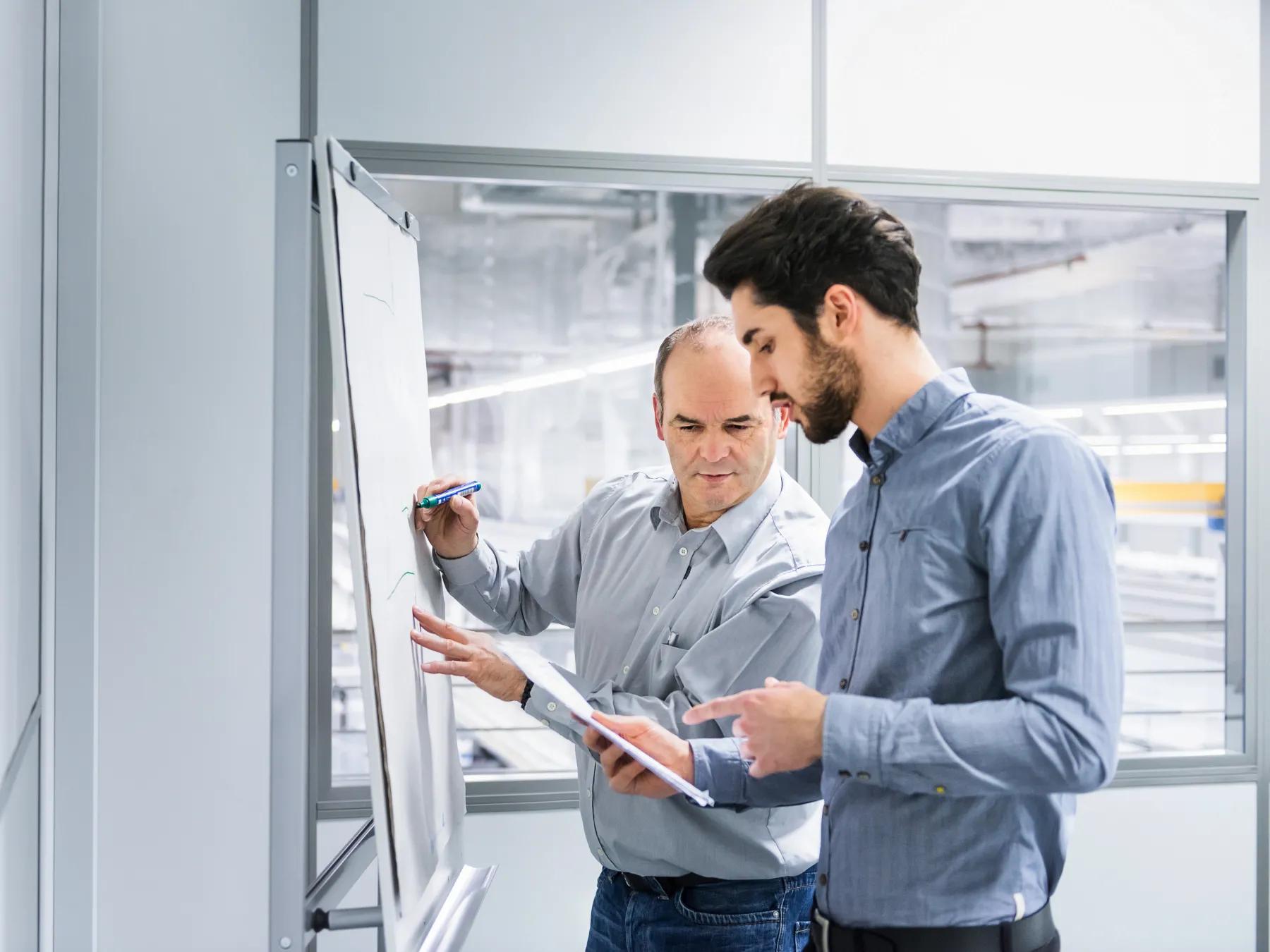
Competences
In increasingly dynamic markets, order-based and batch-size-optimised production and goods distribution require customised just-in-time and just-in-sequence processes.
Whether setting up a new facility or modernising and optimising existing systems - we offer a single point of contact from finding the solution to turnkey handover.
As a general contractor, we design and implement individual intralogistics systems for distribution and production logistics.
The HÖRMANN logistics customer service is available for you on the hotline around the clock, 365 days a year.
Our offer
- We offer you conception, realisation, training and service from a single source.
- You have only one contact partner until turnkey handover
- We ensure an optimal flow of goods and transparent information, shortened throughput times and inventory reductions.
- You receive the most economical solution with transparent costs
- State-of-the-art, future-proof technology guarantees you optimum functionality
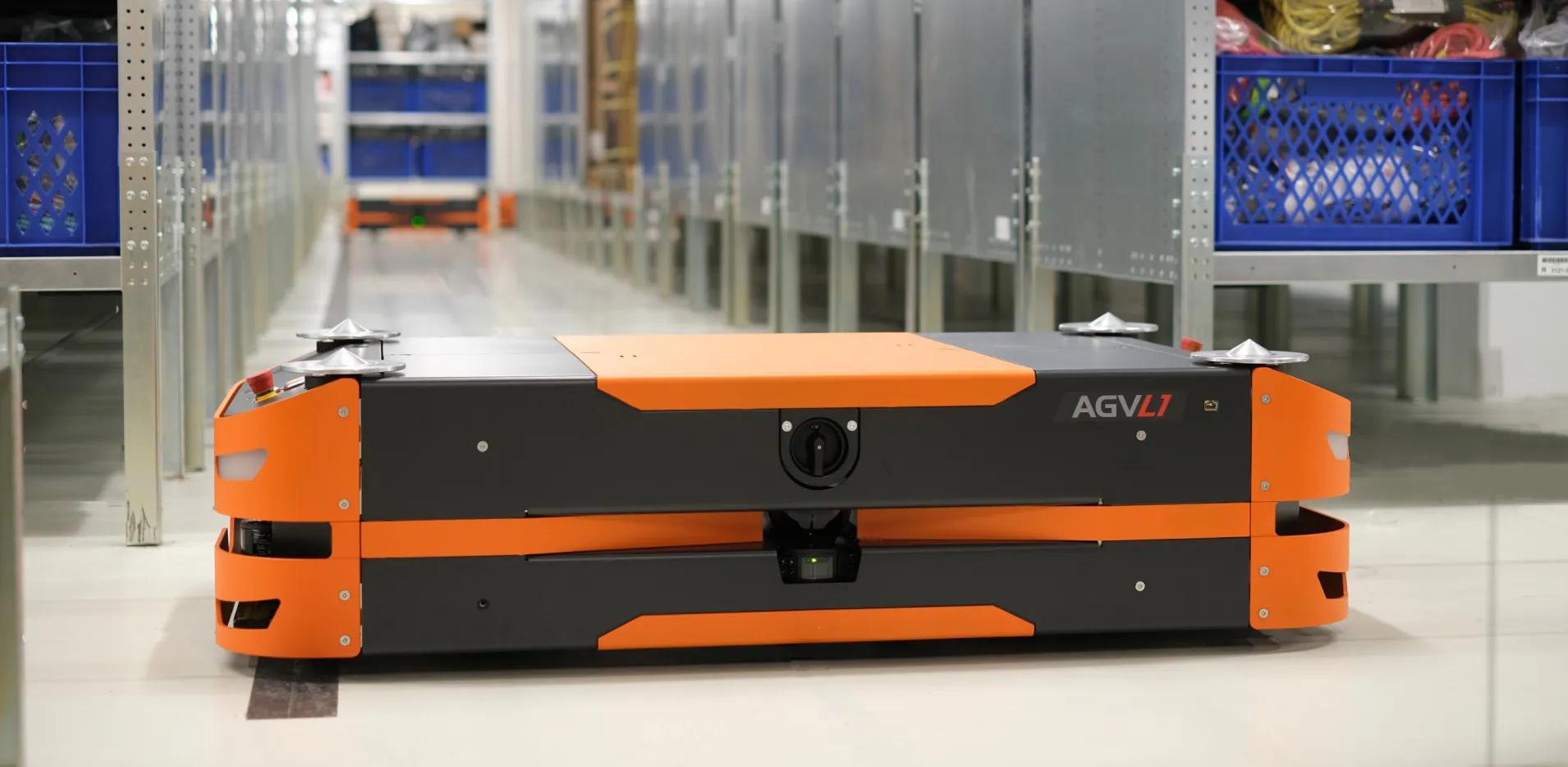
Robotics
Moving Racks solution - goods-to-person (logistics) with robots and racks
Mit kreativen Lager- und Fördertechnikkonzepten sowie innovativen Lagerlogistik-Techniken realisiert die HÖRMANN Intralogistics seit über 35 Jahren maßgeschneiderte Intralogistiksysteme für unterschiedliche Branchen. So auch unsere Moving Racks – mobile Roboter für die Lagerlogistik.
Zusammen mit unseren Tochterunternehmen und Partnern bieten wir dieses und weitere integrierte Systeme für unsere Kunden, bei denen alle entscheidenden Komponenten technisch aufeinander abgestimmt sind und durch unsere eigenen passenden Softwarelösungen optimal zum Einsatz kommen.
Gemeinsam mit unserem Partner SAFELOG GmbH haben wir das innovative HÖRMANN Moving-Racks-System für die Automatisierung von Kommissionierprozessen sperriger und schwerer Güter nach dem Goods-to-Person-Prinzip (GtP) entwickelt.
HÖRMANN Moving Racks
Was sind Moving Racks?
Der Einsatz von HÖRMANN Moving Racks ersetzt oder ergänzt klassische Kommissionierbereiche (Person to Goods) mit hohem Personaleinsatz und langen Laufwegen durch ein effizientes, flexibles System von modularen Regalen (Racks), welche rechtzeitig und in Sequenz den kommissionierenden MitarbeiterInnen präsentiert werden. Der Rack-Transport von den Lagerplätzen (Storage Area) zu den Kommissionierarbeitsplätzen (Picking Area) erfolgt durch mobile Transportroboter (Robot) der Firma SAFELOG. Alle Kommissionierprozesse des Systems werden dabei intelligent durch das HÖRMANN intralogistics System (HiLIS WMS) gesteuert und überwacht, um maximale Leistung und rechtzeitige Auslieferung zu garantieren. Die Schwarmintelligenz der eingesetzten SAFELOG-Roboter ermöglicht optimierte Transportrouten und höchste Redundanz.
HÖRMANN Moving Racks kann als unabhängige Lösung oder gemeinsam mit anderen Lager- und Kommissioniersystemen, wie z. B. AutoStore®, eingesetzt werden. Das HiLIS WMS synchronisiert die Prozesse in den einzelnen Systemen, um die Auslieferung konsolidierter Aufträge aus verschiedenen Bereichen zu ermöglichen.
Die hohe Skalierbarkeit ist ein weiterer Vorteil des HÖRMANN Moving Racks-Konzepts: Das System wächst mit den Anforderungen. Die Anzahl der mobilen Roboter und der Regale kann bei Bedarf leicht an den steigenden Durchsatz und eine wachsende Produktvielfalt angepasst werden.
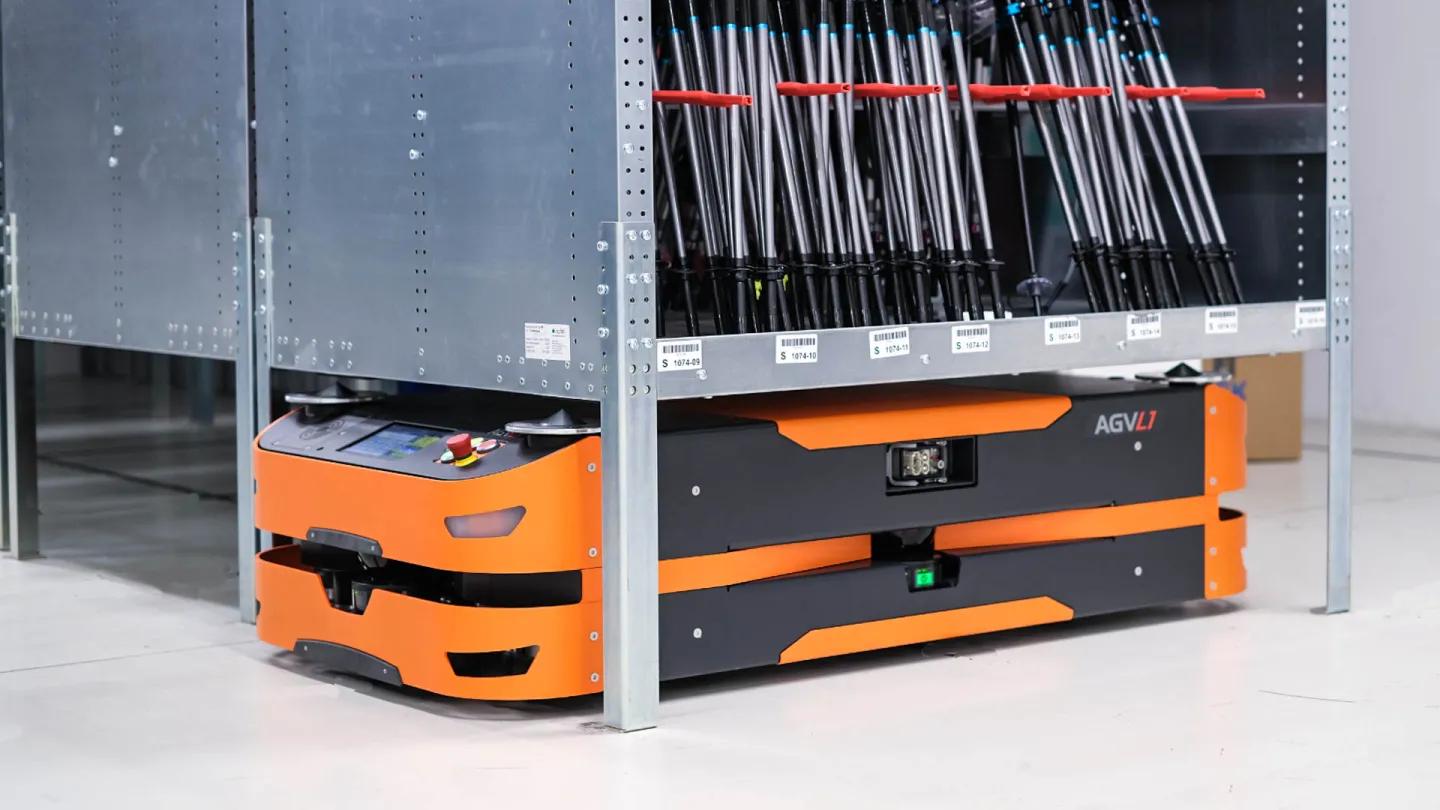
Systemkomponenten von Moving Racks
Storage Area
Der Lagerbereich für alle Güter im HÖRMANN Moving Racks-System besteht aus den einzelnen Racks auf ihren Stellplätzen. Es können unterschiedliche Typen von standardisierten Racks mit verschiedenen Einbauten (z. B. EURO-Palette, Fachboden oder Gitter) kombiniert oder individuelle Racks konfiguriert werden.
Alle Standardracks haben die gleiche Grundfläche von 1280 mm x 900 mm und eine Höhe von bis zu 2500 mm. Die Moving Racks werden in einer Gitteranordnung mit dazwischen liegenden Fahrwegen im Lagerbereich platziert. Die Anordnung des Gitters kann dabei flexibel an verschiedene örtliche Gegebenheiten angepasst werden, um Hindernisse herum oder in abgetrennten Bereichen.
»Zusätzlich können auch Bereiche nahe den Pickzonen für Schnellläufer reserviert werden.«
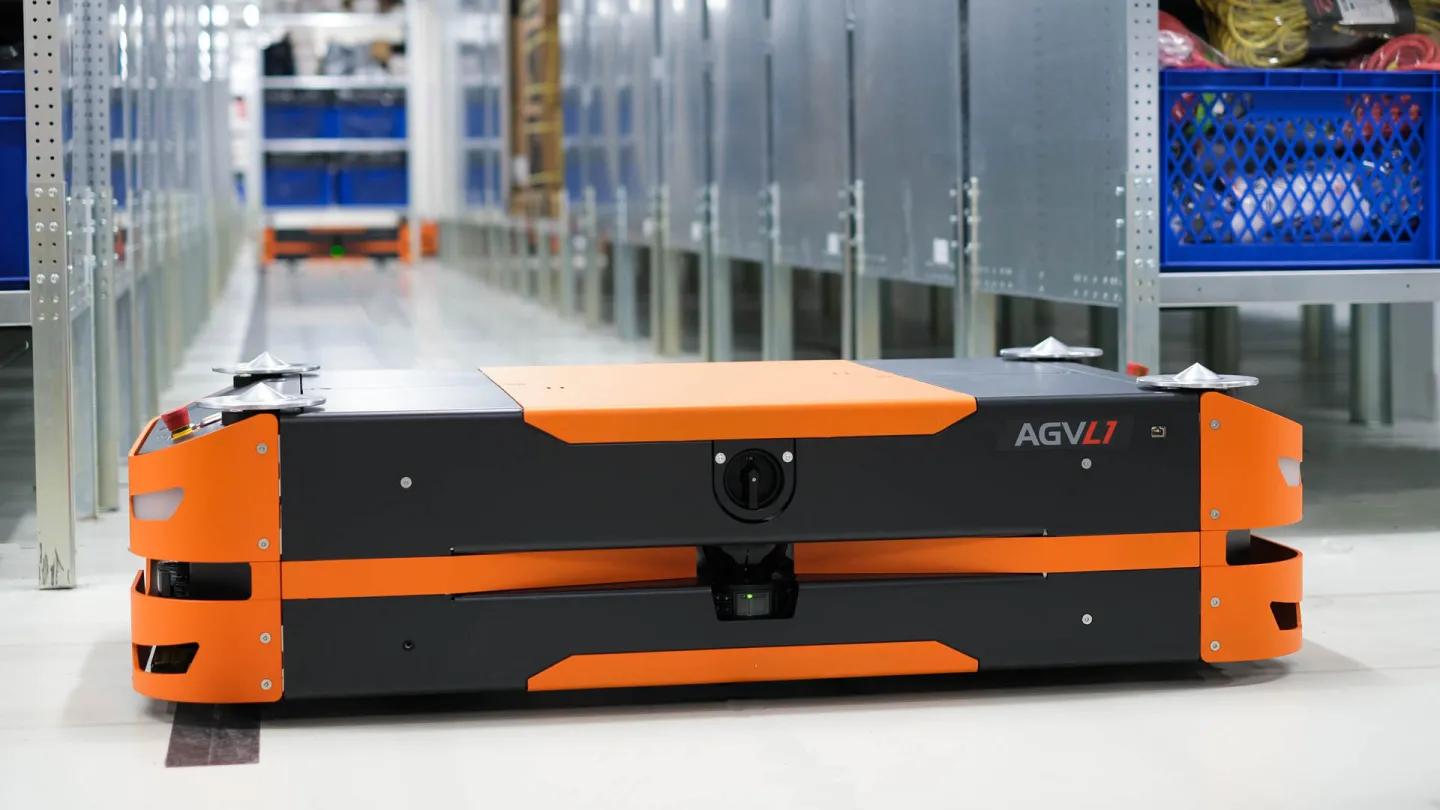
Mobile AGV-Roboter von SAFELOG
Für den Transport der Racks kommen mobile Transportroboter von SAFELOG zum Einsatz. Mit einer Höhe von nur 340 mm eignen sich diese fahrerlosen Transportfahrzeuge zum Unterfahren der Regale ebenso wie für den Transport von Paletten oder Gitterboxen. Das Gewicht des Topload kann dabei bis zu 1.500 kg betragen.
SAFELOG hat für die mobilen Roboter eine agentenbasierte Steuerung entwickelt, mit deren Hilfe die einzelnen Fahrzeuge untereinander sowie mit den umliegenden Produktions- und Logistikanlagen kommunizieren. Diese Schwarmintelligenz der Transportfahrzeuge ist für die Routenabstimmung sowie die Aufgabenverteilung zwischen den Geräten verantwortlich. Ein übergeordneter Leitstand ist daher für ihren Betrieb nicht notwendig. Die Software wird kundenspezifisch auf die jeweiligen Bedürfnisse konfiguriert und ist für die Auftragssteuerung direkt mit dem HiLIS WMS verknüpft.
Um eine möglichst hohe technische Verfügbarkeit des Gesamtsystems zu erreichen, stehen verschiedene Navigationsarten zur Verfügung, welche auch in Kombination Anwendung finden können. Je nach Einsatzgegebenheiten finden Magnetspur, RFID-Tags, virtuelle Spur und Konturnavigation Anwendung oder werden als Hybridnavigationssystem gemeinsam verwendet.
Anbindung an unser HiLIS WMS
Alle Logistikprozesse im HÖRMANN Moving Racks-System werden durch das HÖRMANN intralogistics System (HiLIS WMS) gesteuert. Wir setzen, wie auch für AutoStore®-Installationen, eine speziell angepasste Variante unseres seit 30 Jahren stetig weiterentwickelten WMS ein.
Die gesammelte Erfahrung aus unseren Intralogistikanlagen fließt in die Evolution des WMS ein und ermöglicht für HÖRMANN Moving Racks nicht nur die optimale Steuerung der Picking-Prozesse, sondern auch die Anbindung anderer (automatisierter) Lagerbereiche. Die Konsolidierung von Aufträgen aus manuellen und automatisierten Bereichen ist ebenfalls bereits im HiLIS vorgesehen. Alle Prozesse werden zusammengefasst und übersichtlich im HiLIS Dashboard dargestellt, um perfekte Transparenz zu ermöglichen.
Flexibel erweiterbar
Um HÖRMANN Moving Racks an die Anforderungen vor Ort anzupassen, kann das System modular erweitert werden. Um gestiegene Leistungsanforderungen abzubilden, wird die Flotte der fahrerlosen Transportfahrzeuge (AGV = Automated Guided Vehicle) ohne Anpassung des WMS einfach vergrößert. Um weiteren Lagerplatz zu ergänzen oder zusätzlich abgetrennte Bereiche zu erschließen, können weitere Racks hinzugefügt werden. Die Robots werden durch erneutes Anlernen mit den Erweiterungsbereichen vertraut gemacht. Über die Leistung hinaus kann auch der Funktionsumfang des Systems erweitert werden.
Systeme zur Pick-Unterstützung
Um die kommissionierenden MitarbeiterInnen zu unterstützen, kann die Pickzone durch Pick-by-Light-, Pick-by-Beamer- sowie Place-to-Light-Systeme erweitert werden. Die Konfiguration der Unterstützungssysteme erfolgt gemeinsam während der Arbeitsplatzplanung. Die Systeme können problemlos integriert werden, da das HiLIS WMS bereits für den Einsatz ausgelegt ist.
Multi-Order-Picking - für höhere Pick-Effizienz
Um die Pick-Effizienz weiter zu erhöhen kann das HiLIS WMS für Multi-Order-Picking mit intelligenter Batch-Bildung konfiguriert werden. So ermöglicht das System, mehrere Picks für unterschiedliche Aufträge aus einem präsentierten Rack auszuführen oder sogar mehrere Picks aus unterschiedlichen Quell-Racks auf verschiedene Ziele zu verteilen.
Optimale Rack-Befüllung
Um das Volumen der Moving Racks optimal auszunutzen, kann das HiLIS WMS für unterstützte Einlagerung konfiguriert werden. Die MitarbeiterInnen bekommen so eine visuelle Vorgabe beim Einlagerungsvorgang – entweder über den Bildschirm oder über Place-to-Light.
Qualitätsmanagement- und Inventurprozesse
Für komplexe QS- und Inventurprozesse kann das HiLIS WMS ebenfalls individuell konfiguriert werden. So werden Stichprobenauslagerung oder Warensperrung schnell und einfach ermöglicht.
Wareneingangsarbeitsplätze
HÖRMANN Moving Racks kann auch um dedizierte Wareneingangsplätze ergänzt werden. Die flexible Arbeitsplatzgestaltung und das anpassbare Interface des WMS lassen dabei kundenindividuelle Prüf- und Konfektionier-Prozesse zu.
Übergabezonen für automatisierte Flurförderfahrzeuge
HÖRMANN Moving Racks ist auch auf das Handling und Picking direkt von EURO-Paletten ausgelegt. Hierzu können in Übergabezonen Paletten vom Flurförderfahrzeug an die speziellen Racks übergeben werden. Anschließend werden die Paletten auf den Moving Racks wie Regalracks behandelt.
Moving Racks & mobile Roboter – für mehr Effizient und Flexibilität
Rüsten Sie Ihr Unternehmen für die fortschreitende Automatisierung und nutzen Sie innovative Lösungen für die Lagerlogistik. Mit unseren Moving Racks und mobilen Robotern sorgen Sie für mehr Effizienz bei Ihren Kommissionierarbeiten und erhöhen maßgeblich die Flexibilität.
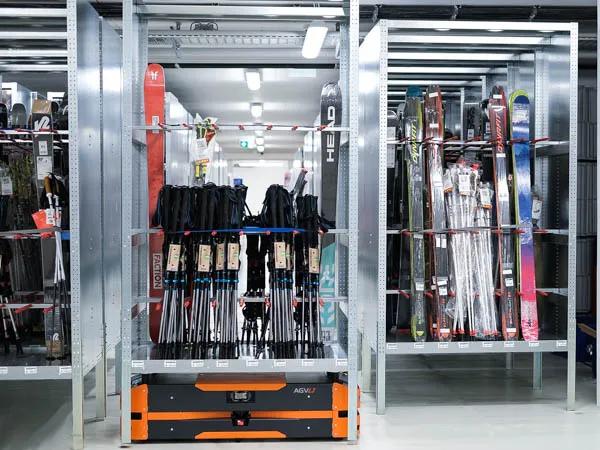
For over 30 years, HÖRMANN Logistik GmbH has been deploying creative warehouse and conveyor concepts as well as innovative warehouse logistics engineering capabilities to build intralogistics systems tailored to the needs of various industries. The outcome includes our Moving Racks – mobile robots for your warehouse logistics.
In a joint effort with our affiliates and partners, we supply our customers with this and other integrated systems characterised by all essential components being technically streamlined and further optimised by perfectly adapted software applications.
Our partner SAFELOG GmbH contributed greatly to developing the innovative HÖRMANN Moving Rack system for automating the process of picking bulky and heavy goods based on the goods-to-person (GtP) principle.
What are Moving Racks?
HÖRMANN’s Moving Racks replace or supplement conventional picking areas (person to goods) and their high manpower needs and long walking distances with an efficient and flexible system of modular racks, which are presented to the picking persons in due time and correct sequence. Mobile transport robots supplied by SAFELOG move the racks from the storage areas to the picking stations. HÖRMANN’s smart Warehouse Management System (HiLIS WMS) controls and monitors all of the system’s picking processes to ensure maximum performance and on-time outbound delivery. The swarm robotics installed in SAFELOG’s robots supports optimised transport routes and a maximum of redundancy.
HÖRMANN’s Moving Racks can be used as a standalone solution or together with other warehouses and order picking systems such as AutoStore®. HiLIS WMS synchronises the processes of all systems to ensure the outbound delivery of orders consolidated from various warehouse areas.
HÖRMANN’s Moving Racks concept also benefits from a high level of scalability. The system will grow with the requirements since the number of racks and mobile robots can be easily adapted to an increasing throughput and the growing product diversity.
Moving Racks System Components
Storage Area
All goods stored in HÖRMANN’s Moving Racks system are kept on the racks at their slots. Options are to combine different types of standardised fixtures (e.g. EURO pallet, shelf or grate) or to configure your own racks.
All standard racks share the same size of 1280 mm x 900 mm and a height of up to 2500 mm. The Moving Racks are arranged in the storage area like a grid plus interlinking transport routes. The grid arrangement can be adapted to local conditions, led around obstacles or moved to separated areas.
"Or you can reserve some space for fast-moving robots near the picking areas."
Maintenance and Charging Areas
Charging stations for mobile robot batteries can be distributed across the storage area and placed near the available power connectors. This will keep charging mobile robots at hand for transport jobs without having to drive extra distances. The robots manage their state of charge themselves and will automatically move to a charging station in due time.
Picking Area
The picking area consists of one or several picking stations and associated buffer stations. Clearly defined transport routes link a picking area to the storage area. Every station can be arranged and equipped as needed.
The standard configuration of a workstation comprises two rack queueing spaces. This allows the next rack to be provided while a picking process is still in progress. For optimised access to the Moving Racks, floor-mounted stop ledges are the only elements separating the provisioning spaces from the working area of the machine system.
Apart from the rack queueing spaces, the workstation contains a desk with a flat screen display unit for showing the HiLIS picking interface and the destination bins of the picked articles. Destination bins can be multi-platform carts, conveyor elements, pallet slots etc.
SAFELOG´s Mobile AGV Robots
SAFELOG’s mobile transport robots are used to transport the racks. Since they are just 340 mm high, these driverless transport units can therefore underride the racks but also transport pallets or pallet cages. The weight of the top load can be up to 1,500 kg.
In order to enable its mobile robots to communicate with one another and any nearby production or logistics equipment, SAFELOG developed an agent-based control methodology for the transport units. The swarm of robots uses this robotics system to negotiate the actual routes and the task of each unit among themselves, thus making a higher-level control station unnecessary. The control software is tailored to the needs of each customer and linked directly to the HiLIS WMS to provide the required task management.
Various navigation methods are provided for separate or combined use to obtain an overall system with a high level of technical availability. They include magnetic tracks, RFID tags, virtual tracks or contour-based navigation able to become part of a hybrid navigation system depending on actual on-site conditions.
The control unit supports omnidirectional movements. A robot can therefore navigate in any direction at any time to ultimately increase its versatility because it can operate in very narrow spaces. It can even turn racks within their slot.
Link to our HiLIS WMS
All logistic processes of HÖRMANN’s Moving Racks system are controlled by HÖRMANN’s Warehouse Management System (HiLIS WMS). Like in AutoStore® installations, the Moving Racks system is based on a specially adapted variant of our WMS that we have been enhancing for 30 years.
The experience we gained from our intralogistics equipment is the main source of further evolving the WMS to enable HÖRMANN Moving Racks not only to optimise the control of picking processes but also to extend to other (automated) warehouse areas. HiLIS also provides the on-board ability to consolidate tasks from manually and automatically handled areas. Bundling all processes and outputting a plain overview to the HiLIS dashboard enables perfect transparency.
Flexible and Extendable
The HÖRMANN Moving Racks system provides extension modules to adapt the system to on-site requirements. Without having to change anything in the existing WMS, the call for increased performance is reflected by simply increasing the number of driverless transport vehicles (AGV = Automated Guided Vehicle). Also, to add further warehouse slots or gain access to detached areas, the system can be extended to include more racks. Afterwards, the robots are re-taught to become familiar with the newly added areas. Extending the system does not stop at the performance but may also involve additional system functions.
Picking process support systems
In support of the picking warehouse employees, the picking area can be extended by pick-by-light, pick-by-beamer or put-to-light systems. Customer-tailored workstation design planning brings all these supporting systems together. Software integration is an easy extra step, since the HiLIS WMS is designed to embed such systems.
Multi-order picking for increased picking efficiency
In order to further increase the efficiency of order picking, the HiLIS WMS can be set up to include multi-order picking and smart batch formation functions. They enable the system to perform multiple picks for different tasks from the same rack or even to move multiple picks from various source racks to different destinations.
Optimised rack filling
In order to make perfect use of the Moving Rack volume, the HiLIS WMS can be configured to support the transfer of products to storage bins. An intuitive GUI workflow or a smart put-to-light system are to tell the employees about what to put where.
Quality management and stocktaking processes
The HiLIS WMS may also be configured to control specific and complex QA and stocktaking processes to support sample retrievals or blocking of goods a quick and easy task.
Goods inbound workstations
HÖRMANN Moving Racks can be expanded by dedicated goods inbound slots. The flexible workplace design options and the adjustable WMS interface support tailored processes of checking and assembling an order.
Zones for transfer to automated floor conveyors
The HÖRMANN Moving Racks system is also designed to support the handling and picking straight from EURO pallets. It may therefore provide zones for transferring pallets from a floor conveyor to specific racks. The pallets on the Moving Racks are then handled like ordinary racks.
Moving Racks & Mobile Robots - for more Efficiency and Versatility
Make your company fit for ever-increasing automation by benefitting from innovative warehouse logistics solutions. Our Moving Racks and mobile robots bring more efficiency to your order picking tasks and substantially increase your versatility.